How to optimize by-product elimination during the continuous vulcanizing process
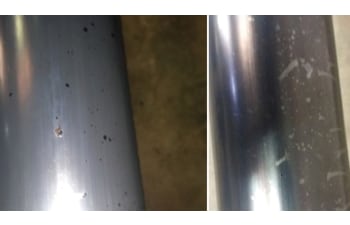
The Continuous Vulcanizing (CV) process is widely used in the production of cables, particularly those with insulating materials like cross-linked polyethylene (XLPE). However, the generation of by-products during CV poses significant challenges, impacting both cable quality and the environment. This article delves into the nuances of by-products, their formation, and the solutions for responsible elimination.
Understanding by-products:
By-products are an inherent aspect of the CV process, particularly in the production of medium voltage, high voltage, and extra high voltage cables, predominantly insulated with cross-linked polyethylene (XLPE). The crosslinking method, often peroxide-based, results in the formation of these unwanted by-products. If not effectively removed, they can lead to cable quality issues.
Challenges in by-product extraction:
Insufficient by-product extraction can manifest in various quality issues, affecting the surface and integrity of the cables. Common problems include those depicted in the picture above, showcasing typical imperfections on the outer cable surface due to inadequately managed by-products.
The environmental dimension:
In contemporary times, by-product elimination is not solely a cable quality concern but has become an environmental imperative. Recognizing this dual challenge, Maillefer has introduced a modern Byproduct Separation (BPS) system, seamlessly integrated with extrusion lines.
Benefits of improved extraction:
Enhancing by-product separation and collection in the CV process yields multiple advantages. These include maintaining optimal production conditions, ensuring stable cooling and heating capacity, reducing maintenance work, and bolstering the environmental and sustainability aspects of cable production.
In the image, a clean BPS unit prior to byproduct extraction (left) and the identical unit afterward, demonstrating effective residue collection (right).
Components of the BPS system:
Maillefer's BPS system, coupled with the Gas ReHeater (GRH) component, emerges as a highly effective solution. The BPS efficiently separates decomposed crosslinking by-products by condensing associated particles in the nitrogen flow. The GRH, within the same gas circulation loop, increases the temperature of the returning gas, injecting it into the curing tube.
Flexible upgrade options:
Both BPS and GRH are offered as enhancement options, ready for seamless integration into any existing CV line, whether it's a Maillefer line or from another source.
Recognizing the diverse needs of CV-line operators, Maillefer offers three main upgrade types for existing CV lines. Whether integrating a complete BPS system with GRH, enhancing an already equipped BPS with the GRH component, or selectively replacing elements for improved results, Maillefer ensures flexibility in upgrading by-product elimination systems.
In the picture, the structure of the BPS loop within a Continuous Vulcanizing (CV) process.
CV cables represent high-added-value products, and any compromise in cable quality directly impacts the bottom line and product image. Effective and responsible by-product extraction is crucial for preserving cable quality and ensuring business success.
For more information about Maillefer’s solutions for cable manufacturing, we invite you to contact the company through the proposed contact methods on the side.