Paving the way for 800V and more
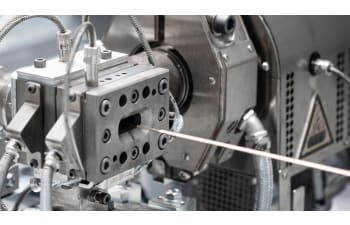
Significant cuts in charging times. Lighter and more efficient cars. The shift from the currently common 400V systems to 800V will bring long-awaited improvements for e-mobility and is expected to accelerate the adoption of electric vehicles worldwide. So-called “hairpins” for stators in electric motors will play a special role in this technological leap. With the worldwide first industry-ready turnkey hairpin extrusion line, Rosendahl is introducing an insulation solution for the safe and efficient use of hairpins at 800V and above.
How can we make e-mobility more convenient for everyday use? Around the globe, researchers and engineers are working tirelessly to address this question. 800V systems for electric cars are on the rise and will overtake 400V systems in the next years. Why 800 volts? Doubling the voltage of electric cars has several advantages. Higher voltage leads to lower current, resulting in less heat generation. A more compact design with thinner and smaller cabling and electrical components in the vehicle becomes possible, leading to a lighter and more efficient car overall. And maybe the biggest advantage: it will significantly reduce charging times.
Overcoming the limitations of 400V with extruded hairpins
The hairpin technology, a winding technology for stators in electric motors, will play a key role in making 800V systems happen. It has become increasingly attractive for automotive applications due to its favorable speed-torque behavior, and high fill-factors. Those qualities help to minimize energy losses and improve the overall efficiency and reliability of the electric motor.
In the majority of today’s applications, hairpins are still enameled. Extruded hairpins have already proven their value in the premium and sports car sectors, though, and are now setting the course for the future. The breakdown voltage achieved with extrusion surpasses enameled insulation by several times, and ensures a safe and reliable power supply, even at higher voltages. Extrusion also outperforms conventional enameling in terms of production speed and energy efficiency by far.
Hairpin extrusion from A to Z
With the newly developed hairpin extrusion line, Rosendahl provides an efficient production process for insulating hairpins using highly resistant polymers. This breakthrough technology will make advanced hairpin insulation accessible to a broader range of manufacturers.
The compact RA-I extrusion line is equipped with Rosendahl’s high-temperature extruder technology and a specially developed crosshead for flat conductors. The complete conductor processing unit comes mounted on a base frame, well guided and stable, to maintain tight tolerances in production. From pay-off to take-up, every line component has been carefully synchronized to meet the high demands of the rectangular hairpin wire.
To attain its distinctive shape, a hairpin needs to be bent multiple times. Its insulation must always adhere firmly and withstand high voltages. The strong material properties that are required for that can be found in the high-performance plastics, such as for example PEEK (Polyether ether ketone). The processing of these polymers requires a deep understanding of the underlying process, and high precision. To achieve uniform wall thickness, the rectangular copper conductor requires exact guiding and material distribution. That is why the new hairpin extrusion line comes with the know-how required to handle the entire extrusion process from A to Z. The end product of Rosendahl’s extrusion solution is a uniformly insulated copper wire, carefully wound layer by layer onto a reel, ready for the next production stages in hairpin manufacturing.
In developing this new manufacturing solution, Rosendahl was able to draw upon years of expertise in the extrusion of high-performance plastics and the insulation of flat cables and bus bars. Building on this strong foundation, the company swiftly adapted its machinery and processes to enter this new product segment. With the introduction of the new hairpin extrusion line, Rosendahl is once more leading the way in the industry, providing high-end solutions for the future of e-mobility.
If you're planning to attend the wire Middle East Africa from September 2 to 4, be sure to visit Rosendahl's booth No. C6A E1D43. Rosendahl will also be among the companies exhibiting at wire China 2023 from September 4 to 7: Stand No. EID43 - and at wire Southeast Asia from September 20 to 22: Stand No. F01.