Upgrade from aluminium oxide
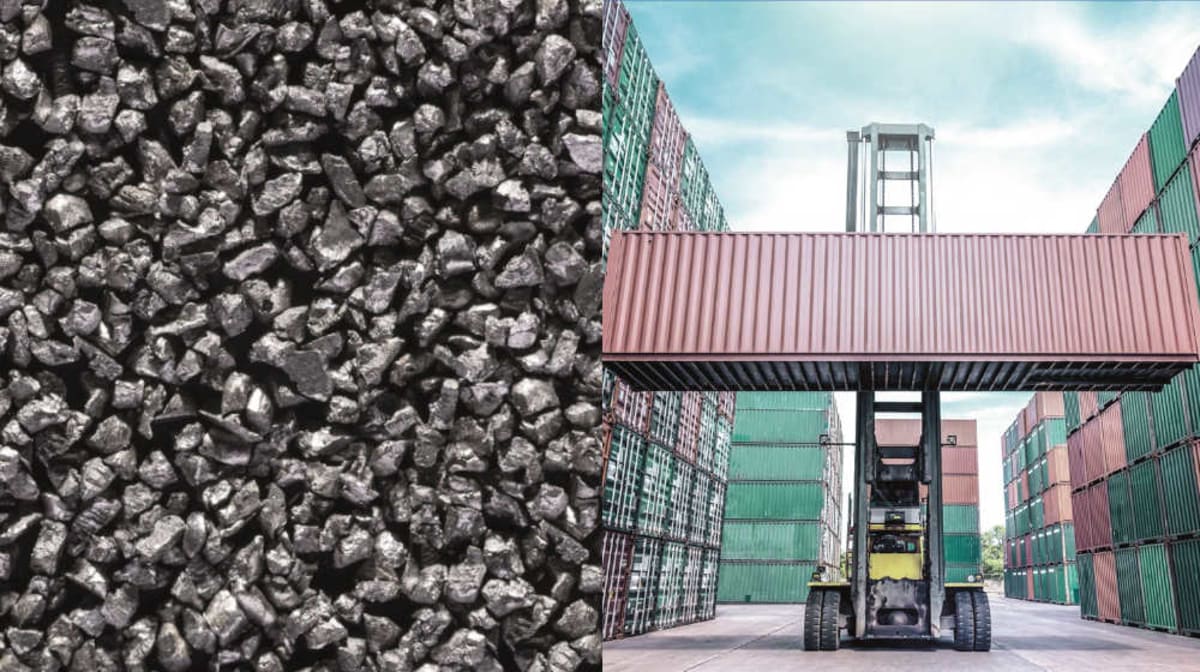
The use of aluminium oxide as a blasting media is under threat from rising prices and lengthening delivery lead-times. Companies struggling with these issues will be pleased to learn that there is an alternative that is widely available at stable prices that also offers better value and reduced costs.
Many forecasters are predicting future shortages of aluminium oxide which is likely to further inflate prices and extend order to delivery times. In addition to the price and availability issues, increasingly users are concerned about the levels of waste and working conditions that result from blasting with aluminium oxide.
AMAGRIT – the sustainable alternative to aluminium oxide
Many blasting operations have already transitioned from aluminium oxide as a blasting medium to Stainless Steel abrasives such as AMAGRIT, from Ervin. AMAGRIT is an angular martensitic stainless steel abrasive, made from recycled materials at the Ervin manufacturing plant in Sprockhovel, Germany.
Good availability and stable prices
With a well-established supply chain, there is good availability of AMAGRIT for Ervin customers and the use of recycled materials in the manufacturing process also makes AMAGRIT a more sustainable option. Together with local manufacturing, the reliable raw material supply helps maintain stable pricing. In use, AMAGRIT typically lasts thirty times longer than aluminium oxide which significantly reduces consumption and overall cost of blasting
Reduced waste disposal
Of course, reduced consumption of abrasives translates directly into reduced waste and cost of disposal. This improves the cost effectiveness of the blasting process and improves the overall sustainability. The very high breakdown rate of aluminium oxide means it can usually only be reused 10 times in a blasting operation, whereas AMAGRIT with its high durability can normally be reused over 800 times!
Improved working environment and blasting quality
The much lower rate of breakdown of AMAGRIT has other benefits. In the blasting room, AMAGRIT generates significantly less dust than aluminium oxide, which makes a better working environment for blasting operators and with improved visibility also comes improved cleaning quality, reducing the risk of over blasting and the need for rework.
Low dust blasting – AMAGRIT (left) compared with aluminium oxide (right)
The high level of dust generated by aluminium oxide abrasives also has a negative impact on the performance of consumables such as dust filters, hoses and nozzles.
Better value
Ervin laboratory tests and data from field trials demonstrates that even allowing for an increased abrasive cost per tonne, switching to AMAGRIT reduces overall blasting costs between 10 and 30 times lower than when using Aluminium Oxide, along with improved repeatability and consistency of surface profiles.
Rust-free surfaces
Even on steel substrates, the surfaces of work pieces blasted with Ervin AMAGRIT are rust-free for up to 72 hours, giving a good time buffer before coating or painting.
One company who switched to using AMAGRIT is Gföllner, a manufacturer of complex container structures often used in very challenging environments. For its products, corrosion protection and surface preparation are vitally important. After testing AMAGRIT as an alternative to mineral abrasives, the company realized they could achieve the required results, while reducing dust, waste and a higher productivity level.
If you would like to know more about how AMAGRIT can be an effective replacement for aluminium oxide in your blasting process, you can reach out to Ervin by using the contact details on the online stand.