Precision grinding: the evolution of Mollificio Romagnoli’s department
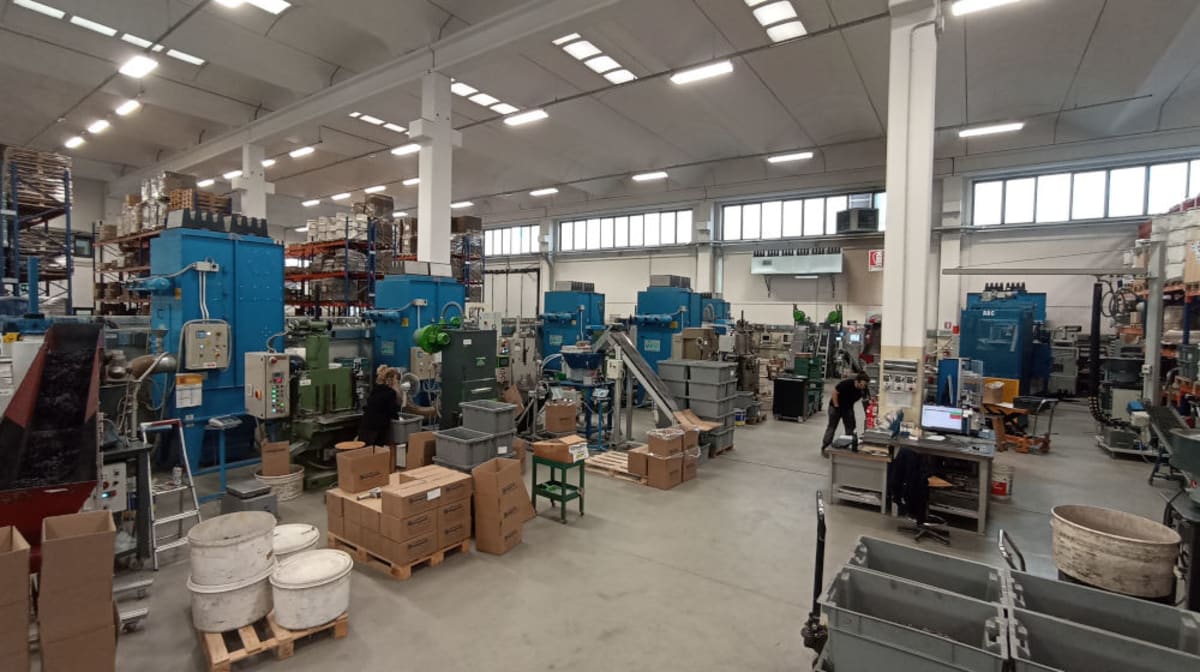
Mollificio Romagnoli, a renowned name in the precision spring industry—specializing in cylindrical and conical compression springs, as well as extension, torsion springs, and custom-shaped components—has recently revolutionized its grinding department, demonstrating a steadfast commitment to innovation and production efficiency.
Over the years, the company has successfully adapted to the demands of an increasingly challenging market, facing targeted investments that have significantly advanced its technologies and production processes.
The grinding department in its early days
Initially, the grinding department operated with a ratio of one grinding machine for every four spring coiling machines, with manual loading and offline settling. While functional, this approach required significant time and resources, substantially affecting order fulfillment times. Recognizing the potential for improvement, Mollificio Romagnoli decided to implement a series of structural and technological upgrades aimed at grinding process optimization.
The grinding department today
Today, the grinding department operates with a ratio of one grinding machine for every two spring coiling machines, with automatic loading and in-line settling systems. With the integration of 13 automatic loaders, the company has eliminated many manual operations, thereby increasing precision and reducing both processing and waiting times.
Among the standout new technologies are diamond grinding wheels, used for precision grinding. These wheels consist of an abrasive disc coated with industrial diamonds, providing exceptional cutting capability and wear resistance. Diamond wheels ensure consistent dimensional accuracy, delivering uniform production quality throughout entire batches and significantly enhancing overall product quality.
Experimentation with new technologies
Mollificio Romagnoli has gone beyond the adoption of diamond grinding wheels, exploring innovative compounds that allow for multiple steel types processes without the need to change wheels. This advancement has significantly boosted production efficiency.
The company has also upgraded its machine shop, introducing next-generation grinders such as multi-head grinding machines, perfect for pass-through processing rather than cycle-based operation. This advancement has led to increased production capacity and reduced lead times.
Monitoring and quality control
The integration of the grinding department with the factory MES (Manufacturing Execution System) ensures continuous operation monitoring, precise batch traceability, and quick response to process variations. In addition, a dedicated inspection station has been implemented for load testing and profile analysis. This station is equipped with an advanced LED3D measurement system, allowing for highly accurate verification of each component's characteristics.
Enhanced logistic efficiency
Mollificio Romagnoli's investments in the grinding department have also significantly improved logistical efficiency. With the implementation of in-line packaging, the company can now package products immediately after processing, ensuring faster and more organized warehouse management.
This series of initiatives reaffirms Mollificio Romagnoli's dedication to pioneering solutions and enhancing its production processes, aiming to deliver high-quality springs and increasingly competitive service. For more information, we invite you to visit the company's online stand and connect with its team of experts.