Fastening systems: the importance of choosing the most effective coating
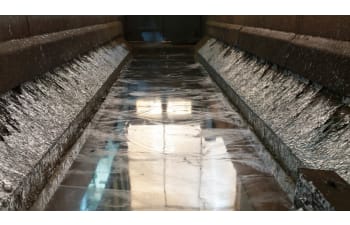
Fastening systems are designed to perform a variety of functions, including holding parts together, distributing loads, and providing aesthetics. In many cases, fasteners are exposed to environmental conditions that can cause wear and corrosion, such as moisture, weathering, chemicals, or salty air. In all these cases, proper coating becomes essential to protect them and preserve their mechanical characteristics and functionality.
Specialinsert, a reference point in the field of fastening systems, illustrates the different types of available treatments, each applied to meet specific needs.
• Zinc coating
Zinc coating is widely used to protect steel fasteners from corrosion by aggressive agents, even in highly oxidizing environments. The corrosion resistance of the galvanized element increases depending on the coating application process, the thickness of the applied zinc, and the roughness of the coated element.
• Chromium coating
Chromium coating enhances the surface, making it less vulnerable to attack by corrosive agents even in aggressive environments. The oxidation of the metallic chromium generates surface passivation, formating chromium oxide that enhances the protection of the coated metal.
• Nickel coating
Nickel coating, which can be performed chemically or electrolytically, enhances the surface characteristics of the treated material, providing hardness and corrosion resistance. The nickel coating process is mandatory if subsequent chromium coating is desired and is performed on steel or brass elements, as well as on plastic components as ABS already treated with copper coating.
• Anodizing
It’s a surface treatment mainly performed on aluminum alloys but also on titanium and other metals suitable for superficial oxidation, creating a protective oxide layer that gives the material high corrosion resistance. Corrosion resistance is directly proportional to the thickness of the generated oxide, the surface roughness of the coated element, and varies depending on the chosen anodizing process.
• Electropolishing and passivation
Electropolishing aims to reduce the surface roughness of the treated element to prevent water molecules or aggressive agents from penetrating the pores of the material. This electrochemical process acts by removing surface imperfections. With subsequent passivation treatment, the treated stainless steel element acquires high resistance to surface corrosion and pitting corrosion.
• Burnishing – Nerinox
The burnishing treatment, which in stainless steels is called Nerinox, is a surface treatment that provides greater resistance to surface corrosion and gives the treated element a black, homogeneous, and intense coloring that can be either glossy or matte depending on the finish of the treated surface.
• Phosphating
It is a chemical treatment that creates phosphate crystals on the surface of the treated carbon steel element. These crystals improve the corrosion resistance characteristics of the steel and reduce the coefficient of friction, facilitating sliding between two fasteners.
Phosphating can be performed with zinc or manganese.
To learn more about the best coatings for fastening systems and much more, we invite you to visit Specialinsert's staff at the Mecspe fair, from March 6 to 8, 2024, in Bologna, Italy, and to contact the company through the references provided on this page.
- Small metal parts •
- Springs •
- Fasteners •
- Various metal parts •
- Screws •
- Small part stampings •
- Rivets •
- Bolts •
- Special springs