Structural and operational advantages of Fasb Linea 2’s integrated subcontracting service
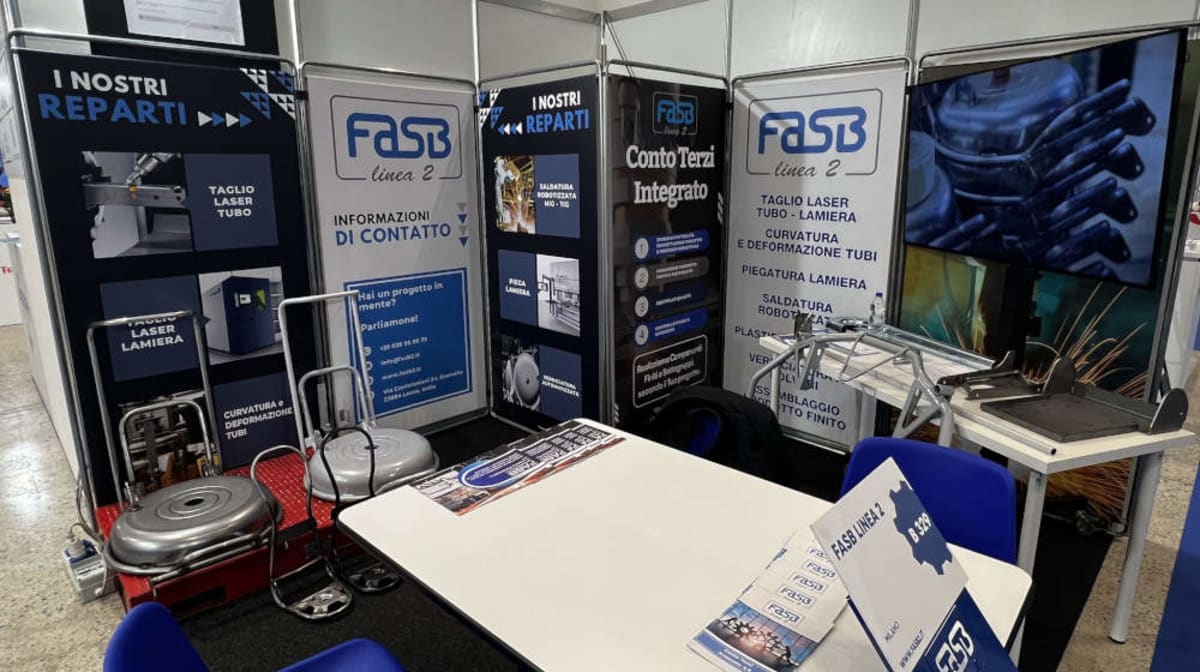
The integrated subcontracting service developed by Fasb Linea 2 is a synergistic model that transforms the supplier into a strategic partner, optimizing the entire value chain through active customer involvement at every stage of production.
This approach integrates engineering expertise, cutting-edge technologies, and industrial processes to generate tangible benefits in terms of efficiency, quality, and sustainability, in full compliance with UNI EN ISO 9001:2015 standards.
Design integration and technical-economic optimization: a synergistic collaboration in feasibility studies
This process begins with a joint feasibility study between Fasb's project team and the customer's technical unit, aimed at identifying the most efficient technical and economic solutions.
This crucial process allows for:
- selecting the most appropriate technologies and the most suitable machinery;
- rationalizing material choices for the required operations (tube and sheet laser cutting, sheet bending, assembly welding, powder coating, and packaging);
- optimizing material thicknesses (up to 25 mm for iron, 20 mm for stainless steel and aluminum);
- defining the best process flow to optimize lead times and production costs.
The design phase also includes 2D/3D CAD simulations to digitally validate decisions before physical prototyping, reducing the risk of errors and material waste.
Flexible modular production with Fasb Linea 2
The modular production system at Fasb Linea 2 ensures efficient management of production batches, from prototypes to medium series (500-5,000 pieces), with changeover times under 45 minutes. This is made possible by a high-tech machine shop, including:
- Laser cutting systems for tubes with diameters ranging from 14 to 220 mm (Adige and Trumpf) and 9-axis bending machines (Crippa and BLM) for tubes from 10 to 80 mm;
- Sheet laser cutting (Trumpf TruLaser1030 Fiber), sheet bending (Trumpf TruBend Serie 5085);
MIG-TIG robotic welding on eight automated rotating-axis workstations;
- Powder coating, performed in a specialized booth capable of handling components up to 2000x800 mm, ensuring high-quality surface resistance.
This operational flexibility allows rapid production adaptation to demand fluctuations while maintaining high-quality standards.
Quality and logistics: customized control and packaging
The subcontracting service model integrates quality control, ensuring high standards through specific control plans. These include dimensional inspections using advanced measuring instruments and non-destructive testing for welds, such as penetrant liquids and ultrasonic testing, to guarantee maximum product reliability.
At the same time, the logistics department develops custom packaging solutions designed to protect components throughout transportation. These solutions are tailored to specific customer requirements, incorporating eco-friendly protective materials, anti-vibration anchoring systems to reduce damage risks, and optimized storage and transport space. This is made possible through the continuous updating of primary and secondary business processes, always aligned with operational workflows.
Innovation, sustainability, and digitalization for an efficient future
Fasb Linea 2 adopts an innovative and sustainable approach by leveraging process digitalization, energy efficiency, and customer collaboration. The information and operational flow is fully digitalized through a next-generation BPM (Business Process Management) system, enhanced by artificial intelligence, optimizing operation management and control.
On the environmental and energy sustainability side, the company has implemented a 192.66 kWp photovoltaic system, consisting of 338 panels, already covering 65% of energy needs. This system is supported by heat recovery from coating processes and intelligent LED lighting with motion sensors. The goal is clear: achieving 100% renewable energy.
Collaborative innovation is another strategic pillar, driven by the CRID (Cost Reduction Ideas Development) project, which promotes co-design with customers. By implementing the VA/VE (Value Analysis/Value Engineering) method, Fasb develops cost-effective solutions, improving product design and identifying lower-impact alternative materials. This approach not only enhances sustainability but also helps customers achieve significant cost savings.
For further details on Fasb Linea 2’s integrated subcontracting service, please contact the company through the references provided on its online stand.