WTM Polyimide Cable Taping Lines, for Double Coating and Sintering
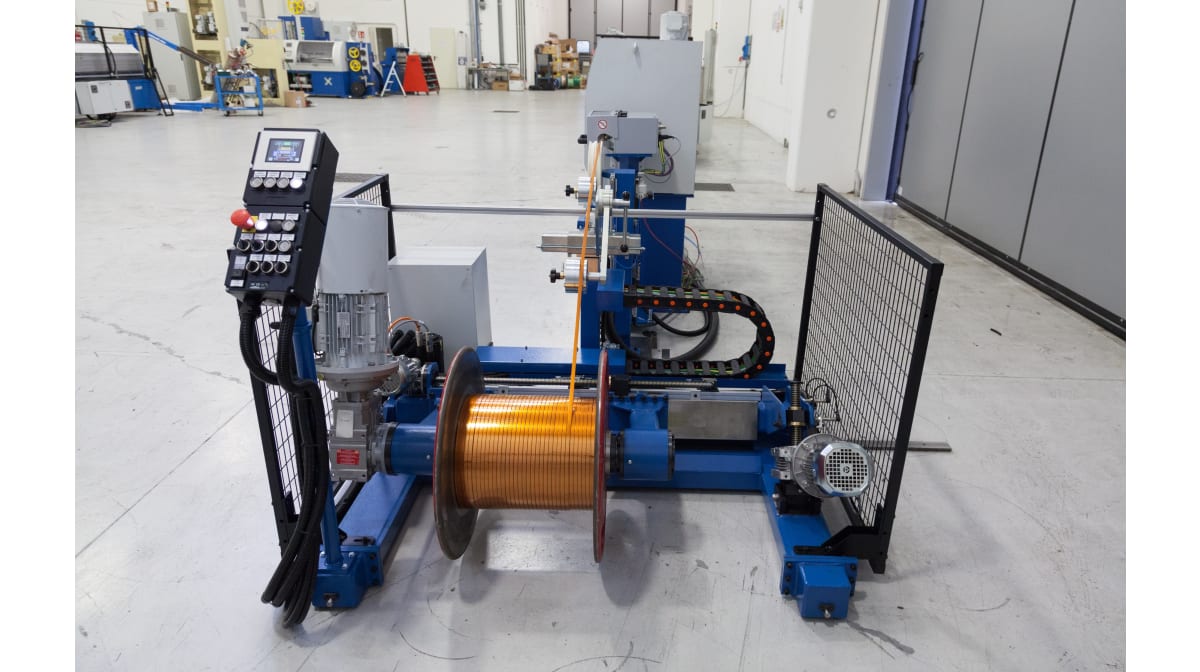
Polyimide is a plastic material that has been used for 70 years in various applications, mainly for its resistance to high temperatures, chemical agents and wear. In particular, the performance of polyimide at high temperatures has made this material fundamental in the sector of specific magnet cables for transformers and electric generators.
Polyimide tapes, precisely wrapped around the conductor and thermoset through a controlled heat treatment, create an effective and reliable insulation that allows the use of these cables in heavy-duty applications, also thanks to the mixing with other components to enhance some specific characteristics.
Considering the added value of the insulation process of these cables, it is important to underline that a polyimide taping line requires high accuracy and control in the various steps, from the treatment of the conductor, to the taping phase up to the thermal process; all aimed at guaranteeing a quality result.
Thanks to the numerous experiences gained in this peculiar type of process, WTM has optimized its taping machines for the application of polyimide tape, to provide its customers with:
- • solutions for the preparation of the conductor;
- • careful management of the tension applied to the conductor, to ensure precise taping;
- • taping heads with dynamic dancer, to maximize the precision of each phase of the taping process, even in the case of conductors with rectangular edges;
- • complex heat treatment systems, also with the subsequent cooling device;
- • in-line taping quality control, using camera systems and spark testers;
- • pay-off and take-up suitable for a smooth and precise cable laying.
This video shows this type of taping machine, equipped with:
- • cable pay-off and take-up unit with traversing movement, that maintains the wire straight, without any deviation from its axis;
- • wire straightening unit with steel rollers and clearing device with brushes, for ensuring the best cable preparation;
- • taping units with taping heads suitable for big cross-wound spools or heavy pads, where WTM dynamic dancer maintains the tape tension constant and stable, guaranteeing a perturbation-free process (highly appreciated in case of flat wires with a high width/thickness ratio);
- • pulling units (combined caterpillar/capstan unit and final caterpillar), for controlling precisely the line speed and the wire tension;
- • fast pre-heating process with high frequency induction heater and following infrared sintering ovens;
- • compacting unit, that allow the complete adhesion of polyimide layers on the conductor;
- • cooling system, with recirculated cold water and air wipers for drying the cable.
- • in-line insulation quality control by means of cameras and spark tester;
If you are a manufacturer of magnet cables, contact us: we will study your technical specifications to design a taping line tailored to your needs.
- Treatment equipment and furnaces •
- Other heat treatment and surface treatment lines
- Machines for electric cables and optical fibers •
- Taping machines •
- Other machines for cables and optical fibers