INVIMEC wire rolling mills: the ideal solution for wire bonding technology
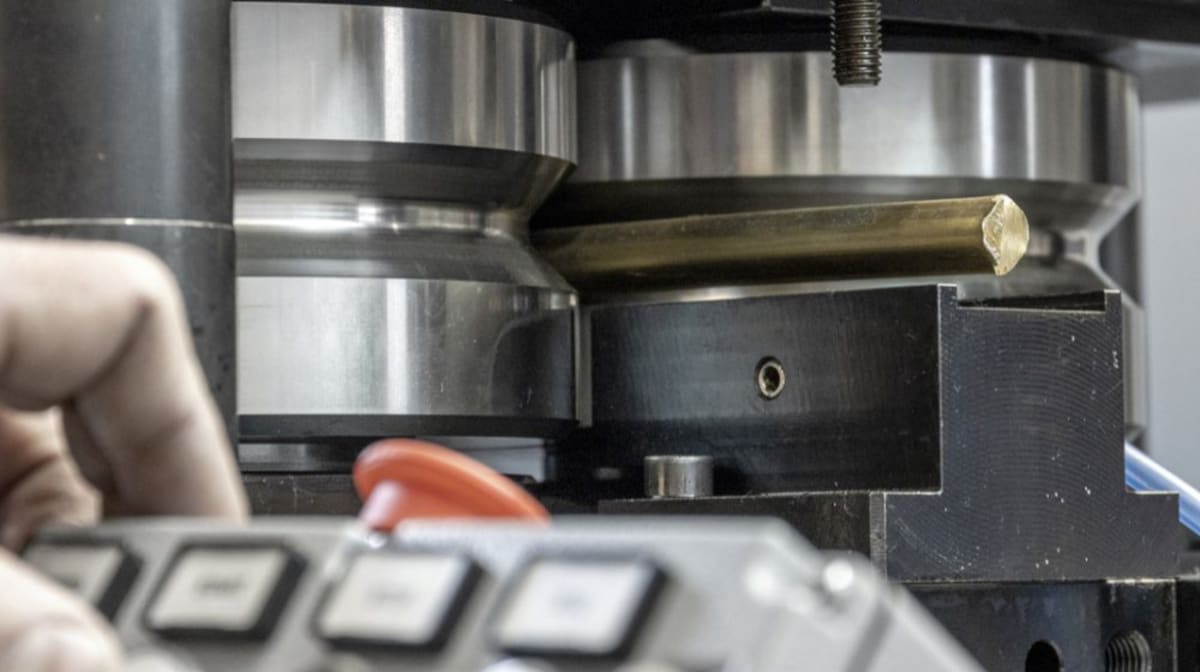
In microelectronic components production, wire bonding is a fundamental interconnection technique. Through thin metal wires, such as gold, aluminum, or copper, connections are made between semiconductor chips and the case or printed circuit board on which they are mounted.
Wire bonding vs. wire welding: key differences
The wire bonding process differs from traditional wire welding in the following aspects:
- dimensions: wire diameters are extremely thin (from tens to hundreds of microns) compared to traditional welding wire (0.5 - 1 mm);
- materials: gold, aluminum, or copper wires are used against tin-lead alloys;
- welding process: specialized machinery applying heat, pressure, and ultrasound versus manual soldering or with soldering machines;
- applications: connection of chip terminals during the manufacture of electronic devices versus joining of components already mounted on printed circuits;
- reliability: high level of precision and quality to withstand the stresses of the final production process versus less stringent critical requirements;
- costs: compared to traditional welding, higher costs due to raw materials and equipment.
Conductivity vs. cost: choosing the right raw materials
Material selection is essential in wire bonding, and here's why:
- gold: excellent electrical conductivity, oxidation resistance, and ductility (very thin bond wires);
- aluminum: slightly lower conductivity than gold and lower costs (standard applications at moderate frequencies);
- copper: cheap material with good conductivity, requires anti-oxidation coatings (low-frequency and low-power interconnections);
- silver: excellent electrical properties for niche applications where maximum conductivity is required;
- metal alloys: combination of metals, platinum acids, or bimetallic coatings.
Invimec presents wire rolling solutions
Invimec specializes in cutting-edge wire rolling mill manufacture, custom-designed for extremely thin metal wires production to be used in the microsoldering process. These rolling mills offer processing quality and dimensional precision, flexibility, and significant advantages over drawing, such as increased mechanical properties of the semi-finished product and the absence of problems caused by drawing stress.
In addition, it is always possible to customize the desired number of cages, integrate loading/unloading systems, choose between coil or bar production, and select software options.
To find the best wire rolling mill for your bonding wire production, contact the Invimec team of experts through the contacts provided.
- Tube machinery ā¢
- Wire drawing machines ā¢
- Cold rolling machines ā¢
- Other machines for tube processing
- Wire tools ā¢
- Tools for tubes ā¢
- Rolling rolls ā¢
- Other tools for wire