Ralc Italia introduces the one and only complete workstation for metal tube processing
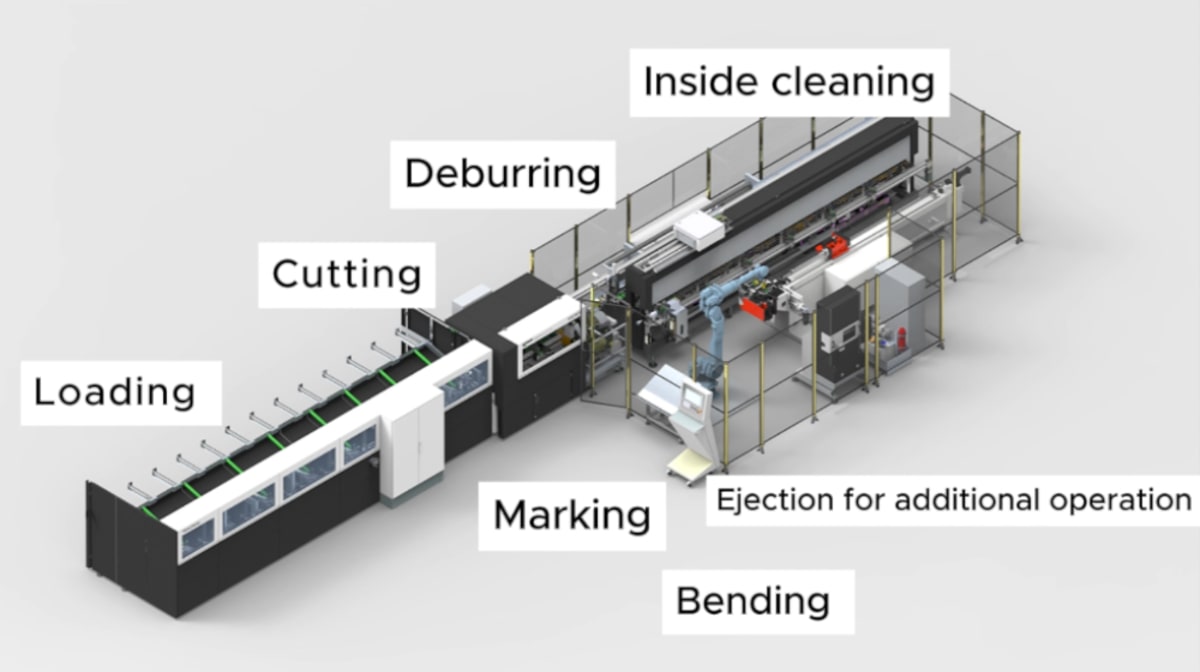
In the metalworking industry, particularly in hydraulic tube production, characteristics such as efficiency, flexibility, and waste reduction are increasingly demanded.
Ralc’s complete workstation, presented for the first time at the recent wire & Tube exhibition in Düsseldorf, is at the center of a market trend which favors flexibility over high productivity. In a market demanding partners like RALC ITALIA, which foresaw the importance of lean manufacturing and production data well before Industry 4.0, the company ensures processes which are efficient, flexible, and minimal waste.
Ralc Italia's response to these needs is represented by a workstation that revolves around the Kronos automatic saw for diameters between 6 and 80mm and its innovative bar optimization system. This complete workstation encompasses multiple tube processing operations in an automatic and continuous workflow.
This solution has among its strengths a remarkable versioning speed, an optimization software containing as much as possible the processing waste and therefore the impact of the raw material on the product cost, and the ability to ensure the traceability of the piece through marking and a wide range of possible subsequent processing.
A single fully automated solution for multiple operations
The strength of this line and its uniqueness on the market is its ability to cut and brush, mark, taper, bend, and unload tubes of different lengths in sequence.
To obtain the finish required by the industry, the line integrates a deburring system that can operate in sequence on lengths between 100 and 6000 mm, different from each other. The system can therefore make the most of the bar optimization software and make subsequent processing independent of the cutting length.
Downstream from brushing, a laser marking unit - capable of engraving QR Code, Barcode, Data Matrix or simple alphanumeric code - has been installed; it’s also possible to request dot peen marking, inkjet or simple labeling.
The line also integrates internal tube cleaning by projectile: an effective, flexible, and inexpensive system for removing chips and machining oils.
The workstation can be implemented with additional processing options such as tapering, bending, and unloading, managed by robots that take the piece downstream of the cleaning operation and bring it to the other units of the workstation.
At the end of the cycle, this solution provides a finished product, already cut, marked, curved, tapered, and perfectly clean inside.
The complete workstation for the tube industry
This workstation is ideal for several applications:
- machine tool manufacturers aiming to bring hydraulic tube production in-house;
- hydraulic tubes manufacturers for machinery, excavators, or those providing services for other businesses, often requiring internal traceability and marking with the customer's logo and article code.
If you are looking for a lean solution for your tube cutting processes, RALC Italia has you covered: contact the experts through the references provided for a consultation and for the necessary customizations.
Watch out for the entire manufacturing process in the video: