The biggest annealer by MFL Group for the world leader in energy and telecoms cable systems
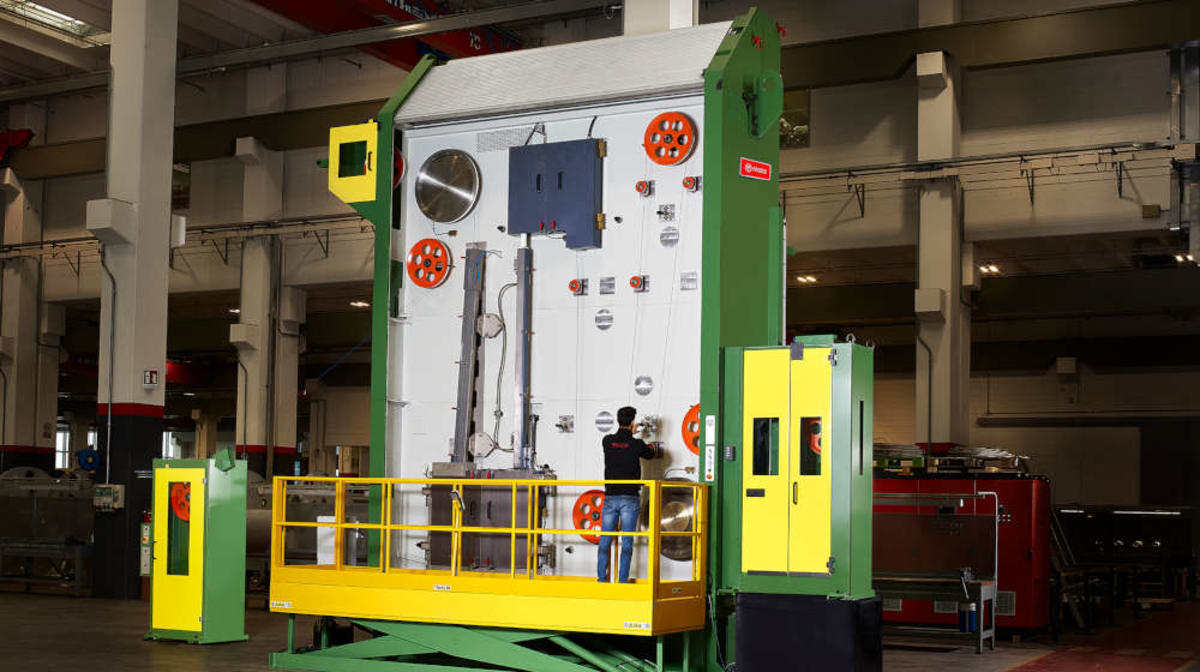
MFL Group is an engineering and manufacturing group of companies with 120 years of experience in wire drawing, stranding-screening-armoring and extrusion machinery for the production of wire, cable and rope.
The continuous search for innovation and new products and services has led several companies worldwide to choose MFL Group as their partners: among them is Prysmian Group, the worldwide leader in the cable industry, that partnered with MFL Group to develop an annealer for copper able to produce wire for large-sized submarine cables.
SUBMARINE CABLE MARKET, AN OVERVIEW
With over 1.3 million kilometers (about 807782.55 mi) of submarine cables laid on the ocean floor, the submarine cable sector is experiencing a significant growth. Submarine cables are used for power and communication, so it is easy to imagine that this trend will continue. The global submarine cable market size was estimated at USD 25.50 billion in 2021 and it is estimated to grow at a CAGR of 6.1% from 2022 to 2030, reaching USD 44.33 billion in 2030. The market expansion is led by the increasing investments in offshore wind farms, efficient power transmission and distribution systems from renewable energy sources, increasing data traffic, and investments by OTT providers.
Other applications of submarine cables include power supply to islands, connection of autonomous grids, supply of marine oil/gas offshore platforms, ShortHaul crossings, and umbilical subsea observatories.
MFL GROUP, SOLUTIONS FOR SUBMARINE CABLES PRODUCTION
Over the last 25 years, the group has made significant investments in developing new products and services, with the aim of offering complete vertically integrated turn-key solutions to non-ferrous cable manufacturers. Each OEM (Original Equipment Manufacturer) has acquired in-house specialized know-how through intense and focused research & development activities to supply innovative solutions tailored to the specific customer product requirements, as well as classic machines and total systems solutions to react to the rapidly changing market demand. In this perspective, MFL Group has significantly expanded its expertise in the wire & cable machinery industry thanks to the acquisition of three companies: CM Caballé, OM Lesmo, Eurodraw Energy. These acquisitions were meant to complement Frigeco strengths and brought extremely valuable intellectual property into MFL’s wire and cable division.
The combination of the different strengths of each brand has fueled exceptionally reliable and field-proven projects for submarine cables production, such as rigid cage stranders, taping and screening lines, armoring lines, annealer for copper and/or aluminum/alloy wire, and planetary strander (where the conductors are not too large).
PROJECT SCOPE: annealer for copper and/or aluminum/aluminum alloy wire
Shifting to renewable sources of energy in marine cable production is especially important. MFL Group has responded to this remarkable trend in the energy transmission field, and can now offer its customers the possibility to build complete plants for the production of these special cables.
Among the company portfolio for submarine cables manufacturing, the AF series stands out for the annealing of copper, aluminum, and alloy wire. The AF 80 provided to Prysmian Group was designed to produce large-sized submarine cables and is capable of annealing copper wire up and over 7 mm diameter at high speed.
Here are some of the key features that have made these annealers the best choice for numerous cables manufacturers:
- single or twin wire;
- wire diameter ranging from 0.8 to 7.0 mm (and over);
- suitable for flat/trapezoidal wire: 35/40 mm2;
- maximum annealing speed of 36 m/sec;
- annealing current of 5000 – 12000 Amp;
- automatic adjustment of annealing current in function of wire diameter and line speed;
- AC motors and flux vector control inverters for maximum precision and low maintenance;
- motor size ranging from 30 to 55 kW AC;
- built-in synchronization sensor;
- annealing capstans diameter of 508, 600 or 800mm;
- 3 annealing shafts without front pipe for minimal maintenance and trouble-free operation;
- preheating section of 9200 mm;
- heating section of 2500 mm;
- multiple jet-stream cooling system;
- wire drying process by compressed air vortex system;
- water-cooled annealing shafts;
- controlled additional air cooling of the brushes;
- second annealing capstan inside Nitrogen enclosure (AF80);
- wire accumulator before Annealer for “zero speed annealing” (AF80);
- cover opens and retracts completely to allow the use of a crane for maintenance (AF80); automatic emulsion valve for wire cooling regulation;
- automatic coolant thermoregulation.
Among the annealers on the market, the AF series was chosen for many reasons, including:
• Ability to anneal wires with a diameter of over 7mm
• High speed and productivity that reaches 6800 kg / h
• Precise regulation of the annealing section, and of the cooling water level
• Hydraulic lift that allows easy wire threading
• Integrated emulsion tank
• Lower investment because it does not require a digging
• Reduction of energy consumption
• Ad hoc system for oxidized wire
• Perfect and constant lengthening of the wire when the machine stops
• Minimal maintenance and trouble-free operation
• Automatic emulsion valve for easy wire cooling setting
If you are looking for machinery to produce submarine cables, we invite you to contact MFL Group through the references on the side.
If you're planning to attend the wire China 2023 edition from September 4 to 7, be sure to visit MFL's booth at Stand No. E1C23. Don't miss the chance to meet MFL Group at wire Southeast Asia in Bangkok (20-22 September): drop by Stand No. J17!
- Wire processing machines •
- Rope-making machines •
- Wire drawing machines •
- Dry drawing machines •
- Pay-off and take-up •
- Wet drawing machines •
- Coilers •
- Various rope-making machines