Metal heat treatment furnaces: 5 questions for Agibi Progetti
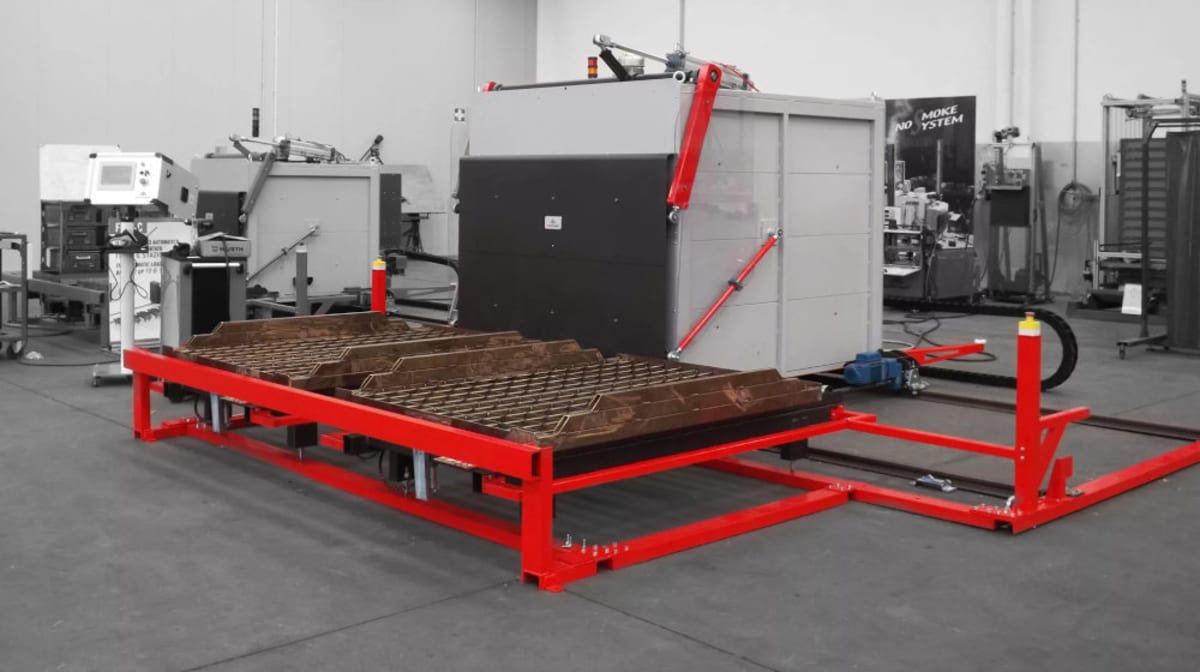
Metal heat treatment furnaces play a fundamental role in the metallurgical industry, altering the physical and mechanical properties of metals through controlled thermal processes. We sat down with Eng. Demis Pigozzi, CEO and partner at Agibi Progetti, to delve into this highly innovative sector where technological progress is crucial.
Briefly, can you tell us about the history of your company from 2001 until today?
Agibi Progetti was founded in 2001 by two cousins, Agostino and Enrico Bortolazzi, with the aim of designing and manufacturing furnaces for metal heat treatments. Mr. Agostino Bortolazzi, having used such furnaces for years as a producer of metal parts for the footwear sector, decided to create his own due to dissatisfaction with their performance. From the outset, our focus has been on reducing heat dissipation, utilizing high-quality materials, and ensuring high temperature uniformity to optimize processes. Continuous research in construction solutions and insulating materials has led to furnaces with thermal efficiency far superior to machines built with traditional technologies using refractory bricks and single-layer insulation. The integration of electronics, automation, and technologically advanced elements in our machines and systems has elevated product quality, securing a niche in the medium-high market segment and driving continuous growth both in production and company structure. Currently, our team consists of 12 employees, 3 partners, and 7 commercial collaborators covering Europe and America (including Canada and Mexico). The presence of many young collaborators makes the company dynamic and responsive to market needs, allowing us to produce both standard products and customized special plants and lines. Our ongoing research to optimize energy consumption and production processes of our clients never stops, and we witness the results year after year.
What is your current production capacity, and what are your main markets?
It is challenging to pin down a specific number as we have a wide range of products, follow many special projects, and the production mix changes every year. To date, we have manufactured approximately 900 machines and systems, reaching a pace of about 45/50 projects annually in recent years. Our main markets include Italy, Germany, France, Switzerland, Austria, Eastern Europe, and the United States, covering the entire European and American basin.
What challenges do you foresee for your business?
For our sector, we have been preparing for challenges related to reducing the furnaces energy consumption and CO2 production during use. These topics are increasingly present in our clients' activities, and in the not too distant future, they may influence the economies of companies. For years, we have been applying cutting-edge solutions and technologies. More recently, we have implemented comparative tests, measurements, reports, and certifications to highlight them objectively. We also don't overlook the automation of processes in recent years: given the difficulty of finding specialized personnel and improving the working conditions of operators, the integration of robots and the implementation of automation have become increasingly popular. These have contributed to creating more autonomous and efficient process lines. We are specializing in applications with robots and developing Plug and Play machines to speed up their integration in the production line.
Will you present these latest innovations at the fair?
Yes, we will be present at the wire and Tube in Düsseldorf from April 15 to 19, booth E02 in Hall 16, to discuss all these topics and showcase our achievements.
Tell us about the best technical result achieved in the last year or the most significant project.
Our greatest technical achievement of last year was the expansion and reorganization of a robotized tempering island with the addition of a tempering furnace. It’s a tempering line with over 15 years of operation and a fixed robot on a base, to which we replaced the old tempering furnace in 2020. In 2023 our client relocated the company and we handled the reorganization of the process and substantial expansion. In the robotized island, we inserted our FCO-C3 chamber furnace for tempering and implemented the robot's seventh axis through a 7-meter travel truck. Furthermore, we developed a new hardware and software supervision system to manage the treatment of large springs autonomously and safely. It was a challenging project that allowed us to venture into new applications and enter the world of robots. The client we collaborated with is the spring maker Adriatica Molle, whom we thank for believing in Agibi Progetti.
Who are your customers today? Which industrial sectors do they predominantly come from?
Our customers are mainly spring manufacturers, but our automation also finds application in metal and plastic stamping companies, as well as producers of technical gasses. Our machines are used in the production of components for the automotive, appliances, furniture, electromechanical elements, aerospace, oil & gas, medical, and any industry where springs are present. In recent years, however, we have recorded an exponential growth in requests for furnaces in the medical sector. These require construction, technological, and control adjustments much higher than other applications, and our over a decade-long experience in the sector allows us to support the customer in choosing the right machines.
We thank Eng. Pigozzi for participating in this interview and we would like to remind industry experts that they can appreciate Agibi Progetti's latest innovations at the upcoming wire and Tube in Düsseldorf from April 15 to 19. The company's team awaits you at booth E02 in Hall 16.
- Wire drawing machines •
- Brushing, descaling and peeling machines
- Lifting and handling •
- Industrial containers •
- Hoppers and conveyor belts
- Treatment equipment and furnaces •
- Stress relieving furnaces •
- Quenching furnaces •
- Tempering furnaces •
- Other heat treatment and surface treatment lines