GF-ELTI unveils the new advancements of H2Burn® hydrogen combustion technology
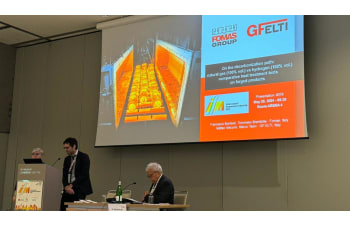
The success of GF-ELTI's H2Burn® technology in comparative heat treatment tests of forged pieces, carried out in collaboration with FOMAS Group, shows the way to decarbonization.
Years of extensive research and testing activities have enabled GF-ELTI to develop H2Burn® technology – high-efficiency burners powered by hydrogen – designed to reduce CO2 emissions in an energy-intensive industry like the steel one.
Thanks to the collaboration between GF-ELTI, a Bergamo-based company specialized in the production of industrial furnaces and plants for the steel industry, and FOMAS Group, a leading manufacturer of forgings, rolled rings (seamless, in any steel and nonferrous alloys) and metal powders, it was possible to test and measure the results of H2Burn® with 100% hydrogen configuration in the heat treatment of forged pieces.
The heat treatment stage plays a key role in the production process of forged pieces. Proving that the use of a hydrogen-fueled plant does not affect the working conditions and at the same time keeps equal mechanical and microstructural characteristics on the piece, compared to heat treatments performed with methane fuel, represents a mandatory examination in the study of the new combustion technology.
FOMAS Group's forged pieces together with its process and quality expertise on one hand, and GF-ELTI's hydrogen combustion plants and technology on the other, created the framework for carrying out two identical heat treatment processes, performed alternately with methane (100 % vol.) and hydrogen (100 % vol.).
The analysis focused on the evaluation of process variables such as temperatures, consumption, O2, CO, CO2, NOx in fumes, as well as mechanical and metallographic tests performed on heat-treated pieces.
The test results showed that, compared with other fuels, the use of hydrogen can reduce CO2 emissions without producing significant differences in qualitative terms.
More specifically, for the same heat treatment process, the time-temperature curves measured inside the furnace chamber and in the pieces proved to be perfectly equivalent, given the same burner power configuration.
The impacts of the two different heat treatment were also evaluated through mechanical and metallographic tests on treated pieces, revealing that the properties are essentially comparable: no differences were found to have an impact at the industrial level, but only a small difference in the morphology of the thin final oxide layer was observed.
Fumes comparative analysis demonstrated that 100% hydrogen combustion completely cancels the presence of CO2 at the expense of increased NOx.
The tests performed thus show the feasibility of a 100% hydrogen heat treatment process on a steel forged piece. The heating of the furnace with H2 requires the use of suitable equipment to allow safe gas management, adjustment of flow rates to achieve equivalent CH4 heating power, and implementation of NOx containment techniques.
In 2020 GF-ELTI launched the H2Burn® project, resulting from the Bergamo-based company's experience, suggesting a blend composed of hydrogen and methane (hydromethane) as a first step towards decarbonization. Today, the skills of a specialized team have made it possible to develop and implement this technology, making industrial plants ready to be fueled with 100% hydrogen.
Driven by its sensitivity to environmental issues, GF-ELTI aims at making hydromethane combustion not just a tool for sustainable development, but also an achievable target from a plant perspective.
Through these tests GF-ELTI and FOMAS Group have significantly contributed to the decarbonization of an energy-intensive industry like forging. Synergies and common sustainability goals make it possible to drive the transformation to green production systems.
The paper "On the decarbonization path: natural gas (100% vol.) vs hydrogen (100% vol.) comparative heat treatment tests on forged products", authored by engineers Marco Teani (GF-ELTI) and Francesca Bonfanti (FOMAS), was presented publicly at the IFM - International Forgemasters Meeting 2024 conference, held in Milan from from 27 to 30 May.
FOMAS Group
FOMAS Group, founded in 1956 in Osnago (LC), is a worldwide key player in forging, ring rolling, and metal powders, specializing in the production of components primarily for the energy, aerospace, defence, and transportation sectors. With facilities in Italy, France, India, China, and the United States, FOMAS Group is committed to providing innovative and customized solutions to meet the technological and quality needs of its global customers. The strength of the Group lies in “mastering the science of metals”, which is evident through cutting-edge processes and continuous research, ensuring the highest quality products. Sustainability is at the core of FOMAS Group's strategy, aiming to reduce the environmental impact of its operations and promote responsible business practices.Thanks to a highly qualified team and the use of advanced technologies, FOMAS Group continues to expand its presence in the global market, strengthening its position as a reliable and innovative partner in the field of metallurgy.
GF-ELTI S.r.l.
GF-ELTI is an Italian industrial Company based in Sovere (BG) that operates internationally in the design and construction of Industrial Furnaces and Heat Treatment Services. The Company, which has been active in the steel industry since the 1960s, is characterised by know-how, design experience, high plant performance, R&D and innovative and sustainable practices. The plants manufactured range from Heating Systems for Steel Works, Heating Furnaces for Rolling and Forging Lines, Furnaces for Heat Treatment, Quenching Systems and Automatic Manipulators. GF-ELTI plants are designed to comply with the most stringent environmental directives and employ the most modern and advanced modelling, simulation, automation, supervision and process control techniques. From the handling of customer requirements to shipment, the entire production chain resides in-house.
- Various plants •
- Treatment equipment and furnaces •
- Reheating furnaces •
- Other heat treatment and surface treatment lines •
- Quenching and tempering plants