Galvanic treatment plant: how it's made
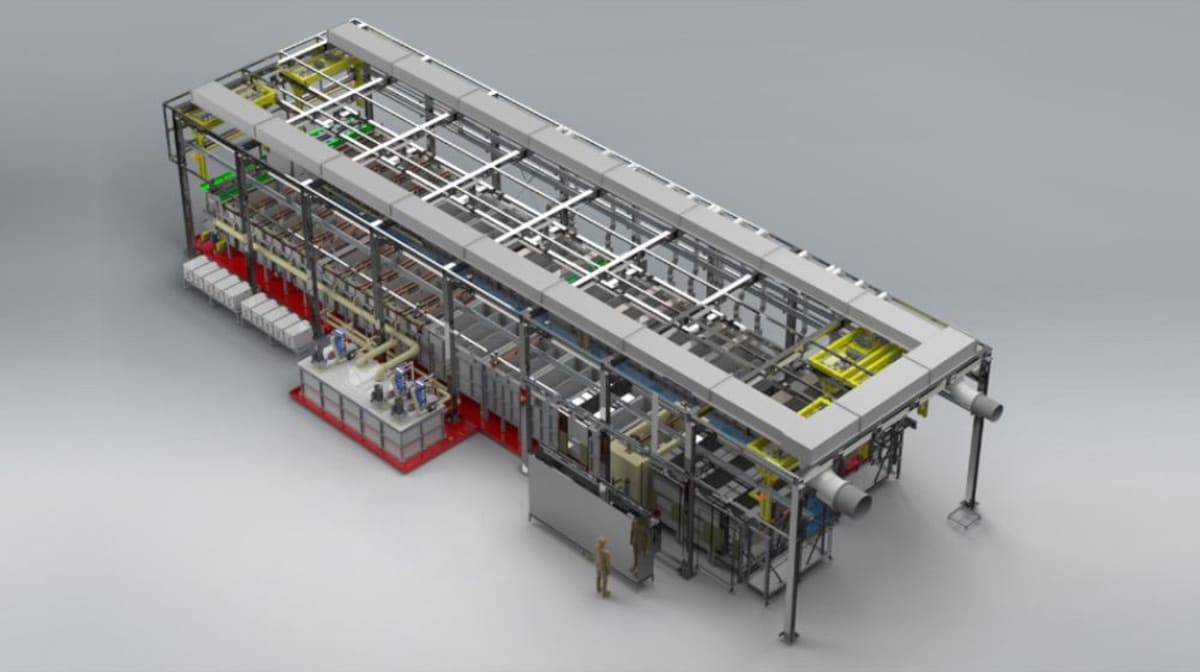
OMIG Srl, a company specializing in the design and manufacturing of galvanic treatment plants, follows a highly structured process to transform what’s just an idea into a concrete project. By working closely with its customers, OMIG optimizes galvanic treatment processes in industries such as automotive, aerospace, precision metal components, fashion, and furniture.
A focus on sustainability and the ability to integrate innovation and flexibility make OMIG the ideal partner for those looking for high-quality surface treatment solutions that enhance productivity.
Let's explore the step-by-step process behind an OMIG galvanic plant and how it’s made.
Step 1: preliminary analysis
The process begins with a detailed technical evaluation, where OMIG examines the materials to be treated, production volumes, and customer requirements. This phase defines the key parameters for the galvanic processes, from electrolytic zinc plating to nickel plating. Every operational detail is carefully analyzed to design a system that ensures quality, efficiency, and sustainability.
Step 2: design
OMIG develops fully customized galvanic plants, tailoring solutions to meet specific production needs. Each project includes:
- advanced mechanical handling systems
- equipped galvanic tanks with high-precision instruments for optimal process control
- cutting-edge software to monitor and regulate treatment parameters
Special attention is given to automation, optimizing processing time and costs in surface finishing operations.
Step 3: construction and assembly
Once designed, the system is built in-house. OMIG manufactures and assembles all components, including structural frameworks, fume extraction systems, and interconnections with wastewater treatment units.
Each plant is rigorously tested to ensure full compliance with quality standards. The final setup is adaptable to various production scales, from small batches to large industrial series.
Step 4: installation and testing
After an initial in-house test, the plant is disassembled, transported, and reinstalled at the customer’s facility. OMIG manages the installation, startup, and final setup, ensuring that every component operates at peak performance.
This phase includes operational testing, allowing the customer to verify real-time production performance, and on-site training for operators and maintenance personnel.
Visit OMIG’s online stand on Expometals.net to explore its product range. The OMIG team of experts is available for personalized consultations—contact them for more information.