MEP system for inert dust: SO.TEC technology for air dedusting
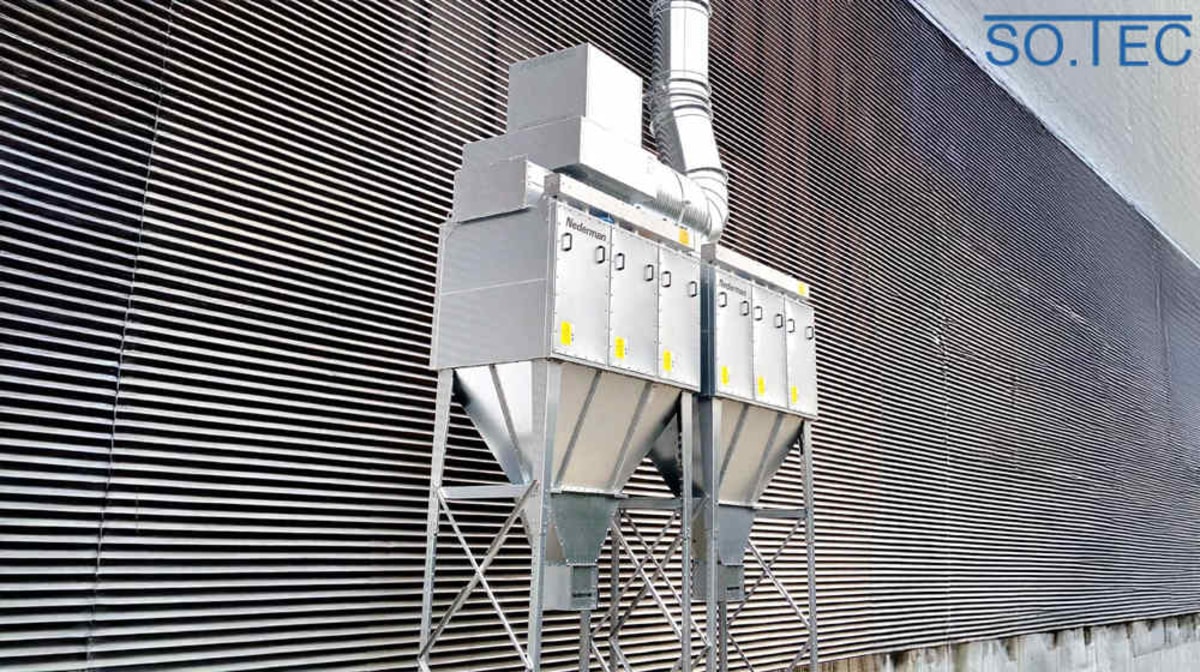
In industrial environments, airborne dust generated by manufacturing processes poses a significant challenge to workplace safety and operational efficiency. Fine dust particles produced by welding, laser cutting, grinding, and tumbling can compromise air quality, damage machinery, and endanger workers' health.
A concrete example of the effectiveness of SO.TEC’s industrial air purification solutions is the installation of an MEP system with a drawer-type filtration unit, designed to manage dust generated from the dry vibration of polyurethane resin and zirconium.
With an airflow capacity of 13,000 m³/h, this bag filter system offers several advantages:
- effective dust removal for inert dust, eliminating explosion risks and the need for ATEX certification;
- lower maintenance costs thanks to automatic compressed air cleaning;
- high energy savings, improving overall efficiency.
Why is industrial filtration essential?
Dust dispersion in manufacturing processes affects safety, efficiency, and regulatory compliance. An effective filtration system is crucial for:
- health protection – prolonged inhalation of fine particles can lead to respiratory diseases and occupational illnesses, especially in the metallurgical, chemical, and composite materials sectors;
- explosion risk prevention – combustible dust, such as aluminum particles, can create explosive atmospheres in environments that lack proper ventilation and filtration;
- equipment protection – dust buildup in machinery can affect production accuracy, increase maintenance costs, and shorten equipment lifespan;
- regulatory compliance – environmental and workplace safety regulations (ATEX, OSHA, Directive 2014/34/EU) impose strict limits on airborne dust concentration, making certified filtration systems indispensable.
SO.TEC dedusting technologies
SO.TEC offers a range of filtration systems, each optimized for specific industrial applications.
Bag and micro bag filters
These filters remove fine dust using technical fabric filter bags, designed to capture particles as small as a few microns. Contaminated air passes through the bags, while dust settles on the outer surface. The automatic cleaning system, controlled by solenoid valves, releases compressed air inside the bags, causing fabric oscillation that dislodges the accumulated dust.
Thanks to their resistance to high temperatures and humid environments, these filters are ideal for demanding processes such as sandblasting, grinding, and metal surface finishing, as well as chemical and pharmaceutical industries requiring strict air quality control.
Cartridge filters
Designed for fine and lightweight dust, these filters use pleated high-efficiency filter media. The large filtration surface allows for high dust retention with minimal pressure drop. Contaminated air passes through the cartridges, where dust collects on the external surface, while clean air is reintroduced into the environment or vented outside.
An automatic cleaning system, managed by solenoid valves, generates reverse compressed air jets, periodically removing dust accumulated on the cartridges’ outer surface.
With their compact and modular design, these filters are ideal for applications with space constraints, such as laser cutting, welding, and chemical-pharmaceutical processes.
ATEX-certified filters
ATEX-certified filters are designed for dust collection in explosive-risk environments, where the presence of combustible dust requires strict safety standards. Their anti-static filter elements capture hazardous particles while preventing electrostatic charge accumulation. Contaminated air flows through the filtration system, where dust settles on the outer filter surfaces, ensuring a safe and controlled airflow.
The automatic cleaning system uses reverse compressed air jets to periodically remove accumulated dust, ensuring continuous operation without compromising safety. Unlike traditional filters, this technology integrates ATEX-certified safety features, such as pressure relief panels, non-return valves, and grounding systems, designed to prevent fires and explosions.
Thanks to full compliance with current regulations, ATEX filters are ideal for high-risk industries, including chemical-pharmaceutical, composite metalworking, and food processing.
Maintenance of SO.TEC industrial dust collectors
To maintain optimal performance, an industrial filtration system requires regular maintenance. SO.TEC recommends:
- performing periodic inspections of the filters;
- regularly cleaning components to prevent dust buildup;
- training personnel on proper usage and safety procedures;
- scheduling inspections and checks to prevent failures and ensure continuous operation.
Discover SO.TEC’s cutting-edge air dedusting technology—contact the company for a customized consultation!