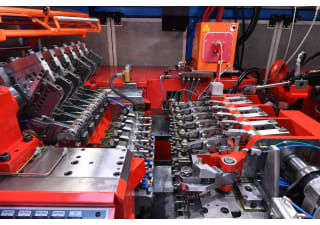
How are fasteners made? The main manufacturing processes for screws, bolts, and nuts production
General introduction about fasteners
Fasteners have become an integral part of everyday life. Typical fasteners include screws, bolts, nuts, and washers that come in a wide variety of different shapes. Fasteners are generally made from coiled wire or round bar stock made of cold upsetting steel, alloy steel, copper alloys such as brass and bronze, aluminum alloys, titanium alloys, and nickel-base alloys.
More information about fasteners and their applications here >>>
Manufacturing methods
Generally speaking, there are three main ways to produce a fastener: cold forging, hot forging, or machining. Based on the type of fasteners to produce and the metal they are made from, one method may be more preferable to the others. Standard fasteners are commonly manufactured through cold forging (without heating up the material).
Cold forging
This method enables the high-speed manufacture of net shape parts or near net shape parts with favorable mechanical properties and a high-quality surface finish. Another benefit to cold forming over hot forging or machining is work hardening. During cold plastic deformations, the material’s crystal structure undergoes profound changes, becoming stronger and more resistant. The result is a finished part with better physical and mechanical properties. The process does present some limitations, in that parts with bigger diameter need more pressing force to be shaped. Therefore, other methods may be preferable.
The performance of cold forming machines depends, among other things, on the size of the fasteners to be manufactured. Some can reach a speed of 300 parts per minute or even more. The smallest screws and bolts, used for electronic components and clockworks, have a diameter of less than 0.5 mm, while the largest cold formed screws have a diameter of around 30 mm.
Hot forging
Hot forging is the common method for producing bolts with large diameters starting with a thread size of approximately M36 or more, and a length of approximately 300 mm and more. The bar stock is heated up to high temperatures to make the material more malleable and then fed into a forging press. The temperatures are determined by the bar material, geometry, and tolerances. With this process, it is possible to manufacture even complex shapes and high degrees of forming. Hot forging is also the process of choice for manufacturing fasteners made from nickel-based alloys and titanium alloys. A distinctive feature of hot-formed fasteners is their raw surface structure. Hot forging has its own disadvantages, as it is very time-consuming.
Unlike machining (which we will tackle in a second), cold and hot forming are chipless processes.
Machining
Machining is a manufacturing technique in which a metal is cut into a desired final shape and size by a controlled material-removal process. This method is really only suitable for non-standard fasteners and small quantities, as it generates a great deal of metal swarf, and it is also time-consuming.
Cold forging of screw and bolt blanks
Usually, cold forging machines are horizontal presses working at room temperature. The starting material of the cold forming process is coiled wire, which is paid off by a feeding device, straightened and then fed into the press. There, the wire is sheared according to a fixed length. The resulting bars, called blanks, are picked up by a transfer device and transported through several workstations. Each station consists of a punching tool and a forming die. Each step forms the material closer and closer to its final shape, until the part matches the shape of the last die. This process is also called “heading”, and the result of this is a screw blank with a head and a shaft.
Thread forming
A specific device is responsible for the cleaning and polishing of the blanks.
The next step is threading. The thread is usually formed in a thread rolling machine, where the parts are placed between a pair of flat dies – one fixed and the other one carrying out a reciprocating movement – or between 2-3 rotating cylindrical dies. The dies have grooved surfaces which correspond to the desired thread to be formed. Thanks to this combined movement, the dies form the thread on the headed blank. The former method allows processing several hundred screws per minute, while the latter offers the possibility to create overlength threads.
Thread rolling is a cold forming process: it generates smooth, precise, and uniform external threads, without altering the integrity of the microstructure. Therefore, it improves the mechanical characteristics of a fastener.
A thread can also be made by means of a tap or a screw stock. This process is called thread cutting, as it involves the severing of the material’s grain structure.
Cut threads can be manufactured to virtually all specifications, however many manufacturers prefer thread rolling, as rolled threads are often much smoother and
resistant to damage during handling.
Generally speaking, threads are manufactured before heat treatments (e.g. hardening and tempering).
Cold forming of nuts
Nuts are square, round, or hexagonal metal blocks with a threaded hole which matches the external thread of an appropriate bolt. The blanks can be sheared from wire and shaped in a cold forming press (s. above). Nuts may also be manufactured by cutting a blank from a hexagonal rod and drilling a threaded hole in it. The internal thread is cut on a nut-tapping machine with a screw tap.
Heat and surface treatment
In many cases, fasteners undergo heat treatments, which affect their microstructure and thus their physical properties, such as strength and ductility. The process steps depend on the metallurgical characteristics. Steel fasteners, for example, are heated to a specific temperature according to the carbon content, and they are kept at this temperature for a specific time. Subsequently, the parts are quenched in water or oil to increase their strength and hardness. The parts are then reheated – to a lower temperature – to achieve greater ductility with fewer distortions in the microstructure. A heat treatment line for steel fasteners, for example, features washing, degreasing, hardening, quenching, washing, annealing and dyeing stations. Usually, these lines are mesh belt furnaces, where fasteners travel at a certain speed through the various stages.
Sometimes, surface treatments may be required as well. For instance, special coatings may be applied to improve fasteners’ properties. Case-hardening is used for tapping screws and self-drilling screws, for example. The screws are heated and kept for a certain time in a carbon-rich atmosphere. The carbon seeps into the surface, increasing the local carbon content. Then, the screws are quenched and thus hardened. As a result, the surface of such screws is rather hard while their interior remains ductile.
Additionally, special coatings may be applied to improve corrosion resistance. Such a coating is achieved, for example, by galvanization.
After the processing is done, fasteners undergo a final cleaning step and are then ready for packaging and shipping.
Literature
IFI Book of Fastener Standards. 10th ed.
Industrial Fasteners Institute. Independence OH, 2018.
https://www.indfast.org/shop/display_products.asp?cat=8.
Taylan Altan, Gracious Ngaile, Gangshu Shen: Cold and Hot Forging: Fundamentals and Applications, volume 1. ASM International, 2004.
ISBN 13: 978-0-871-70805-2
https://b-ok.cc/book/808081/ea1282
Metal Forming Handbook. Schuler GmbH. Springer, 1988.
ISBN 978-3-642-63763-6
eBook ISBN 978-3-642-58857-0
https://www.springer.com/gp/book/9783642637636
The information has been compiled by Dipl.-Ing. Konrad Dengler, technical journalist and translator specialized in industrial topics.