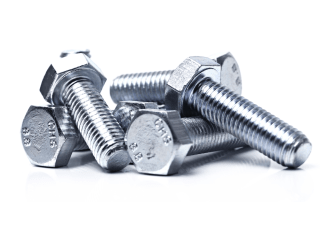
What is galvanizing? Definition, types, and applications
Galvanizing involves applying a zinc layer to metal products like wire, ropes, sheets, fasteners, pipes, and steel profiles. This surface coating improves aesthetics, extends lifespan, and provides protection against oxidation.
These processes involve chemicals or techniques that modify the surface properties of the material. Methods range from chemical treatments to immersion in electrolytic baths, each governed by specific standards.
Galvanizing is ideal for corrosion protection, offering durable, cost-effective, and versatile coverage. It is widely used across sectors such as construction, infrastructure, automotive, household appliances, and in industries like marine, oil & gas, chemical, and manufacturing.
Differences between hot-dip galvanizing, cold galvanizing, and electroplating
There are several galvanizing processes, each offering unique advantages. The right choice depends on factors such as product size, geometry, operating environment, and the level of protection required. Zinc layers can be applied using different methods, with the most common being hot-dip galvanizing, thermal spraying, and electroplating.
Let’s explore the three primary methods: hot-dip galvanizing, cold galvanizing, and electroplating.
Hot-dip galvanizing
Hot-dip galvanizing offers the highest level of corrosion protection, with durability lasting up to 100 years. Before galvanizing, metal items undergo pretreatment processes like pickling to remove rust or scale, followed by washing to eliminate iron and acid residues. These steps ensure a uniform surface, preventing defects. The metal is then immersed in a bath of molten zinc at high temperatures, forming a thick, uniform zinc layer. This provides excellent corrosion resistance at a relatively low cost. While increasing the zinc layer adds a few microns to the piece, hot-dip galvanizing is not suitable for small or complex-shaped products, as it may cause deformation.
Cold galvanizing
Cold galvanizing, also called metallization, involves applying zinc-rich synthetic resins in a process similar to painting. As with hot-dip galvanizing, parts must undergo pretreatment, including scale removal, degreasing, and surface cleaning. Cold galvanizing is ideal for small or complex-shaped items, as it avoids deformation and provides a more uniform aesthetic finish. However, it offers lower corrosion resistance compared to hot-dip galvanizing.
Electroplating
In electroplating, items are first pre-treated with degreasing and pickling, followed by a second degreasing step. After preparation, the metal is immersed in an electrolyte solution containing dissolved zinc salts. When an electric current is applied, zinc ions deposit onto the surface through a process called electro-deposition. The item then undergoes a passivation bath, a crucial step that forms a thin film to enhance corrosion resistance once dried.
Each galvanizing method has unique characteristics, but all aim to protect the metal surface. Regardless of the galvanizing method, uniform coverage is key for complete protection. Electroplating is especially popular for steel and ferrous alloys, offering reliable protection with a lower environmental impact than other techniques.
Black, yellow, and bright zinc plating: applications in the fasteners industry
Beyond the galvanizing techniques we have discussed so far, there are some zinc plating variants worth noting. During the final passivation step of electroplating, the product takes on different colors based on the metal used as a protective sealant.
Bright zinc plating: This treatment gives the metal a bluish hue, commonly seen in products like screws, nuts, washers, self-tapping screws, self-drilling screws, and lifting accessories.
Yellow zinc plating: With its pale yellow tint, this finish is often chosen for aesthetic reasons and is suitable for a wide range of items, from small components like screws and bolts to larger structural elements. Its primary role remains corrosion prevention, as seen in wood screws.
Black zinc plating: Achieved through black passivation and an additional sealing phase, this finish enhances both the appearance and corrosion resistance of metal items. Products like self-tapping and self-drilling screws treated with black zinc plating are widely used in sectors such as window frames, furniture, mechanical construction, woodworking, and automation.
Galvanizing in the fasteners sector: norms and standards
Galvanized products in the fasteners industry must adhere to legal standards. For hot-dip galvanized fasteners, the international standard UNI EN ISO 1461 specifies the minimum zinc layer thickness for compliance.
The average required thickness is:
• At least 45 microns for steel thickness < 1.5 mm
• At least 55 microns for steel thickness between 1.5 mm and 3.0 mm
• At least 70 microns for steel thickness between 3.1 mm and 6.0 mm
• At least 85 microns for steel thickness > 6 mm
Electroplating is regulated by the UNI ISO 2081 standard, effective from April 12, 2018. This standard outlines the electroplating process and its variants, specifying the requirements for zinc electroplating on iron or steel, including additional treatments. UNI ISO 2081 is closely related to UNI ISO 4520, which defines the criteria for passivations.
Other metal products, such as wire or pre-galvanized sheets, fall under separate regulatory frameworks.
Hot-dip galvanizing: how to measure zinc layer thickness compliance
Accurately measuring the zinc layer thickness is crucial to ensure product quality before shipment and market release. There are four primary methods for assessing the thickness of hot-dip galvanizing:
• Using magnetic coating thickness gauges
• Stripping and weighing
• Weighing the item before and after galvanizing to calculate the weight increase from the zinc layer
• Optical microscopic observation
Literature
Electroplating: how it works
What is galvanizing: a comparison of types
Black galvanizing: what are its characteristics?
Galvanizing thickness: standards, dimensions, and durability
The information in this article was compiled in collaboration with Univiti, an international benchmark in the wholesale of standard and custom screws and bolts, with a catalog of more than 20,000 items.