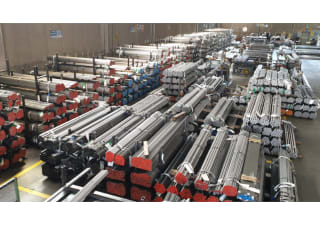
Metal bars and profiles: fundamental differences, manufacturing, and applications
Metal bars and profiles, spanning various dimensions, are integral to daily life, serving either as finished goods or as raw materials for diverse end products.
Definitions: cross-section differences that define bars and profiles
According to the European Standard EN 10079, steel bars are defined as hot-formed bars with a consistent cross-section throughout their length. Round bars are long products with a circular cross-section varying in diameter. Profiles feature square, hexagonal, or octagonal cross-sections, with sides typically measuring 8 mm or more for squares and 13 mm or more for hexagons. Additional long products with irregular cross-sections include beams, channels, angles, and rails. Various metals, including steels, non-ferrous (NF) metals like copper and aluminum - as well as their wrought alloys - along with titanium and nickel-base alloys, are available in the form of bars and profiles in a range of dimensions and sizes.
Production: all about bar and profile manufacturing
Production begins with cast ingots as the starting materials, which undergo plastic deformation through hot rolling, occasionally followed by cold rolling or extrusion processes.
Hot and cold rolling processes
Hot rolling occurs at temperatures above a metal's recrystallization point, while cold rolling is conducted at room temperature, below this point. In the case of steel, for example, ingots are initially heated in a rotary furnace to approximately 1,200 °C, a process lasting several hours. Heated ingots are then fed into a rolling mill, typically comprising multiple consecutive stands with grooved rolls. Here, they pass through the gaps between the rolls (2 or more) in each stand, a process requiring 9 to 15 passes for shaping. Steel ingots are usually hot-formed at temperatures ranging from 800 to 1,150 °C. These elevated temperatures ensure high formability during plastic forming while facilitating permanent crystal formation, known as "recrystallization," within the microstructure. As the ingots undergo plastic deformation under high pressure from the rolls, they adopt the shape of the gaps. With each pass, the cross-section of the ingots diminishes while their length increases and the rolling speed accelerates. In the final pass, ingots obtain their final shape, sometimes featuring specific surface patterns like protrusions on concrete-reinforcing bars (rebars). After hot rolling, bars or profiles are swiftly cut by a flying shear into manageable lengths of e.g. 50 m for handling on the cooling bed. Here, they undergo cooling and inspection and are subsequently cold-cut to their shipping length. In certain cases, shaped pieces may undergo a secondary rolling process at room temperature (cold rolling), enhancing their dimensional accuracy.
The extrusion process
Extrusion is a forming process where ingots are heated to forming temperature and pressured through a die opening to shape bars and profiles. Primarily used for aluminum and copper, it allows for intricate cross-sections. The resulting bars and profiles, up to 60 meters long, are then cut to the desired length.
After-treatment and finishing operations
Certain bars and profiles undergo heat surface treatments to adjust their material properties. For example, railheads are often heat-treated in-line to improve wear and impact resistance. Finishing operations include straightening, cold-cutting to the ordered length, marking, and inspection. Furthermore, round bars can be reduced to smaller diameters by drawing them through one or more drawing dies.
Simulation technologies
As bar-rolling mills employ various layouts, rolling processes are meticulously planned, simulated, executed, and monitored using computer-aided simulation systems. Computers aid in designing roll passes, scheduling, and controlling complex operations, while specialized software tools gauge the productivity and Overall Equipment Effectiveness (OEE) of rolling lines.
In the picture, the GMS-S inline geometry measuring system by MSG Maschinenbau, intended for straightness and twist measurement of profiles.
Applications
Hot-finished bars, supplied in straight lengths rather than coils, distinguish themselves from rods. Hot-rolled round steel bars, prioritizing strength over precision, are used for construction and other applications. Conversely, cold-rolled round bars, prized for precise dimensions and surface finish, are essential for braces and frameworks. Round steel bars serve myriad end products, including car axles, rotor and crankshafts, piston rods, steering gear shafts, pistons and wheel bearings, gear racks, differentials, and e-mobility components. Like wire, round bars can be transformed into technical springs, hooks, fastening elements, and reinforcing mesh. Steel profiles, featuring square cross-sections and a side length ranging from 6 to 130 mm, are prevalent in residential and commercial buildings, fences, and security doors. Extruded aluminum profiles find utility in window and construction profiles, while copper profiles with cross-sections in various shapes are among others used for DC motor collector profiles and AC motor rotor bars. In the case of aluminum, its lightweight often plays a decisive role, and copper's excellent electrical and thermal conductivity enhances its applications.
Literature
Siddhartha Ray: Principles and Applications of Metal Rolling
Cambridge University Press
https://assets.cambridge.org/97811070/76099/excerpt/9781107076099_excerpt.pdf
Siddhartha Ray: Principles and Applications of Metal Rolling
Heritage Institute of Technology, Kolkata, April 2016.
https://www.cambridge.org/us/universitypress/subjects/engineering/industrial-manufacturing-and-operations-engineering/principles-and-applications-metal-rolling?format=HB&isbn=9781107076099
Youngseog Lee: Rod and Bar Rolling. Theory and Applications
First published in 2004; eBook published in April 2014.
https://www.taylorfrancis.com/books/mono/10.1201/9781482276695/rod-bar-rolling-youngseog-lee
https://www.routledge.com/Rod-and-Bar-Rolling-Theory-and-Applications/Lee/p/book/9780824756499
Zygmunt Wusatowski: Fundamentals of Rolling
Elsevier, October 2013
https://books.google.de/books/about/Fundamentals_of_Rolling.html?id=ftggBQAAQBAJ&redir_esc=y
Aluminum Information Portal: Aluminum Extruded Profiles
https://aluminium-guide.com/en/aluminium-extruded-profiles/
The information has been compiled by Dipl.-Ing. Konrad Dengler, technical journalist and translator, specialized in industrial topics.