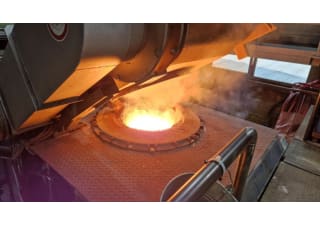
Shot blasting: meaning, definition, and origin
Shot blasting is a surface preparation and metal finishing process in which small abrasive particles— often called shot or media—are propelled against a surface at high velocity. By striking the surface, the blasting media removes rust, paint, mill scale, or other contaminants, creating a uniform surface roughness that enhances adhesion of paints, coatings, and other protective layers.
Who invented shot blasting?
Shot blasting was not invented by a single person but evolved over time thanks to several contributors. Its foundations trace back to the late 19th century, with Benjamin Chew Tilghman’s development of an adjacent process: sandblasting. As manufacturers manifested the need for faster, more reliable metal surface cleaning, various innovators began experimenting with different abrasive materials and propulsion systems (eg. compressed air or mechanical wheels). It is during the early 1900s that the first patent related to shot blasting machines was developed.
Then, in the 1920s, John F. Ervin made a significant breakthrough by introducing cast steel blasting shot and grit, which proved to be far more durable and effective than sand, thus laying the groundwork for modern shot blasting technology.
Over the years, turbine-driven blasting systems and continuous material refinements turned the process into an essential operation in fields such as automotive, aerospace, and heavy machinery.
Shot blasting vs sandblasting vs shot peening: what’s the difference?
Shot blasting and sandblasting are both part of the broader category of abrasive blasting, which involves propelling abrasive material against a surface to clean, smooth, or strengthen it.
To this end, sandblasting and shot blasting may look similar, but they serve very different purposes. The former relies on compressed air to shoot fine abrasives, making it ideal for softer materials (wood, glass, or ceramics). The process historically relied on silica sands, while modern methods now use safer expendable abrasives like garnet, crushed glass, or metallic abrasives such as steel or stainless steel grit & aluminum oxide to reduce health hazards. While the latter uses metallic abrasives to strip, clean, and strengthen metal surfaces, and generally relies on centrifugal wheels to propel recyclable metallic abrasive.
Another form of abrasive blasting is shot peening, which involves bombarding a surface with small spherical media. This process induces compressive stress in the surface, preventing cracks and extending the lifespan of components like gears, turbine blades, and springs.
Why is shot blasting done? Benefits and applications
The primary goal of shot blasting is to clean surfaces and prepare them for coating, welding, or further processing. This process can be cost-effective and easily scaled: metallic abrasives are often recyclable, and automated shot blasting machines allow for fast, high-volume processing.
As a result, shot blasting is widely used in the automotive industry, where car manufacturers often use shot blasting to prepare chassis parts. In aerospace it is used to reinforce critical components like turbine blades, while foundries and metal fabrication shops utilize it to remove residual sand from castings. Another field of application is shipbuilding and construction, where shot blasting is used to treat beams, hulls, and other structural elements before applying protective coatings.
The shot blasting process: how does it work?
The shot blasting process is carried out using two main propulsion methods.
Wheel blasting: uses high-speed wheel blasting equipment to fling abrasives at the workpiece. This technique is especially suited to large-scale or high-volume operations.
Compressed air blasting: which employs compressed air to direct the shot through a nozzle, offering greater flexibility and precision—particularly useful when treating smaller parts or components with complex geometries, or very large parts unable to pass through a wheel machine.
The process utilizes shot blasting machines, which come in various configurations to accommodate different needs. Tumble blast machines or rotary drums agitate smaller items to ensure all surfaces receive equal treatment. Table systems can rotate heavy or large objects in front of the blasting stream. Conveyor-based solutions handle continuous flows of parts in high-throughput settings, passing them under multiple blast wheels for comprehensive coverage. Meanwhile, manual cabinets let an operator precisely target the blast stream, making them ideal for detailed work on limited quantities or specialized components. For larger scale air blasting, large rooms or chambers are used.
Process stages
Regardless of the propulsion method, the workpiece is placed in a blast chamber or booth, where the media is launched at controlled velocity and angles. A powerful dust collection system removes debris and fractured particles, ensuring unobstructed visibility and a high-quality finish. The media then cycles through a separator that filters out broken shot and contaminants, returning only intact abrasives back into the system. This closed-loop design allows shot blasting to minimize material consumption, maintain consistent quality, and uphold environmental standards.
Overview of shot blasting materials and media
Blasting media generally fall into two main categories—round shot and angular grit—but variations exist within each type.
The cast steel blasting shot was pioneered by John F. Ervin in the early 20th century and revolutionized the industry by offering a more durable and consistent alternative to sand. Its mostly spherical shape is effective for cleaning and preparing surfaces without excessively cutting into them.
Steel blasting grit, produced by crushing or fracturing shot, generally features sharper edges that deliver more aggressive abrasion for tackling heavy rust or scale. Both shot and grit can be recycled multiple times due to their high durability, reducing media consumption and overall costs. In applications where iron contamination must be avoided, stainless steel shot or grit ensures a non-ferrous finish.
Beyond metallic abrasives, non-metallic materials such as aluminum oxide, glass beads, and ceramic particles are available for precision work, particularly when introducing ferrous material is undesirable. Each type of abrasive features a distinct level of aggressiveness, so the ideal choice depends on the substrate’s properties and the desired outcome.
Importance of media quality
High-quality abrasives ensure a consistent surface profile and reduce the creation of dust or embedded contaminants. Abrasives with uniform size, shape, and hardness deliver predictable results and minimize wear on turbines or nozzles. In contrast, non-metallic and low-grade metallic media can degrade quickly, generate excessive dust, and cause uneven finishes, undermining paint adhesion and overall part integrity. Many industrial users periodically test their media, using equipment such as the Ervin Spot Check Kit — checking for particle size distribution and shape—to maintain an optimal balance that supports cost-effective, high-quality output.
Conclusion
In conclusion, shot blasting is a proven method for cleaning, preparing, and strengthening various materials, particularly metals like steel and aluminum. By maintaining the right balance of shot blasting media, equipment design, and process parameters, businesses can consistently produce high-quality, contamination-free surfaces ready for coating or further fabrication. The process delivers an optimal blend of efficiency and precision, ensuring durable, reliable outcomes in even the most demanding industrial settings.
Literature
https://www.ervin.eu/shot-blasting-guide/
The information presented in this Wiki was compiled in collaboration with Ervin GmbH, developer of steel and stainless steel cast abrasives and gold standard in this industry since 1920.