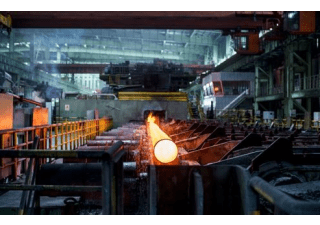
Tube and pipe manufacturing
Tubular steel products are manufactured mainly by two different methods resulting in seamless pipes or in welded pipes. The starting material is always a hot steel billet. In the first case, the hot billet is processed by punching, hot rolling and stretch-reducing rolling into a seamless tube. In the second case, the hot billet is shaped into a plate or a strip by hot and cold rolling; the plate or strip is then bent and the edges are sealed by welding.
Production of seamless steel pipes
Seamless steel pipes are made from a hot round billet and get their shape through three main working steps: at first, the hot billet is transformed into a hollow shell by piercing (along its axis) and hot rolling, or by extrusion; the following stage is the elongation, which simultaneously reduce the diameter and wall thickness of the pipe shell. Finally, the tube gets its final shape through hot rolling, cold rolling, or drawing. The main manufacturing methods for seamless steel pipes are the Mannesmann plug mill process, the Mandrel Mill process, and the extrusion process.
The technique for piercing hot solid ingots through cross rolling invented by the Mannesmann brothers in 1885 is generally considered the starting point of the industrial production of seamless pipes. The so-called Mannesmann plug mill process starts with a round steel billet heated in a rotary hearth furnace. After heating the billet, it is pierced by a cone-shaped mandrel and fed into a rolling plug mill, where a pair of conical shaped rolls operates in the opposite direction to the material flow. With this cross piercing process, a thick-walled hollow shell is generated. With a second rolling operation called “pilger rolling process” the hollow shell is then elongated and its wall thickness reduced. In this way, a seamless steel pipe is formed.
The Mandrel Mill Process also starts with a preheated cylindrical steel billet. The first step is called rotary piercing. The billet is cross-rolled between two barrel-shaped rolls. As a result of the high-tensile stress, the axis of the billet tears open. Simultaneously, the billet is pierced along its axis by a water-cooled tool. In this way, a hollow pipe shell is formed. Afterward, the pipe shell must be transferred to a floating mandrel mill which consists of several rolling stands and pairs of rolls, as well as a set of mandrel bars. The mandrel bars are inserted into the pierced pipe shell, which is conveyed to the rolling station. The mandrel bars act as a control mechanism, creating an intermediate standard outside diameter (OD) and a controlled wall thickness. After progressing through the mandrel mill, the mandrel bars must be removed from the tube shell, cooled-off and returned to the feeding station, ready for another shell. The pipe is then reheated and further reduced to specific dimensions by a stretch mill. The final tube is then cooled-off, cut, straightened and subject to finishing and inspection before shipment.
The pipe extrusion process is carried out in extrusion presses. The starting material, a hot billet, is forced by a ram through an extruding die which has a smaller cross-section than the billet. The extruded metal is compressed between the ram and the die. The exterior profile of the pipe is formed by the die, while the interior profile is formed by the ram. With this method, numerous profiles can be obtained.
Production of welded steel pipes
Welded steel pipes are made using steel plates or coiled steel strips. In the first case, the plate is rolled into a round section with the help of a bending machine. Then, the adjoining edges are sealed together by longitudinal welding. In the second case, the strip is rolled into a circular section with the help of funnel rolls. Depending on the forming process, the strip is bent either along its longitudinal axis (and the edges are longitudinally welded) or in a helical form (and the edges are spirally welded).
There are two types of processes for the production of welded pipes: pressure welding and fusion welding. The most common pressure welding methods are the Fretz-Moon process, direct current electric resistance welding (ERW), low frequency (LF) electric resistance welding, high frequency (HF) induction welding, and high frequency (HF) conduction welding. In the ERW process, a pipe is manufactured by cold-forming a flat sheet of steel into a cylindrical profile. The two edges of the steel cylinder are heated through electrical current and sealed together without the use of welding filler material. The most common fusion welding processes are submerged arc welding (SAW), and gas shielded welding, such as MIG or TIG.
Tube drawing
Tube drawing is used to resize large diameter tubes into smaller ones. It is performed at room temperature by pulling the tube through a die. In some instances, the required size may not be obtained directly from the rolling mill, therefore cold drawing can be used. In this process, the tubes or pipes are coated with an oxalic and soap solution to reduce friction while drawing. The tube or pipe is pulled over a drawing bench using die plugs. The result is a high-quality tube with precise dimensions, good surface finish, and added strength. For such reasons, this process is widely employed in the metalworking industry. There are different tube drawing technologies. In many cases, a mandrel is used to prevent buckling or wrinkling in the tube.
Finishing
The rolled pipes and tubes are cut to the required lengths and cleaned. A heat treatment is performed to remove stresses that may occur during the previous forming and welding phases. After the heat treatment, the tubular products are pickled, descaled, and straightened. Moreover, they can be galvanized and marked for identification. Based on the final application, their ends can be threaded or beveled by machining. After a set of testing and quality checks, the tubes are finally ready for packing and shipping.
Literature
Rolf Kümmerling, Klaus Kraemer: Pipe Manufacture – Seamless Tube and Pipe. Chapter 15. In: R. Winston Revie (ed.): Oil and Gas Pipelines, John Wiley & Sons, Inc., 2015.
Print ISBN: 9781118216712
Online ISBN: 9781119019213
DOI: 10.1002/9781119019213
https://onlinelibrary.wiley.com/doi/book/10.1002/9781119019213
https://doi.org/10.1002/9781119019213.ch15
The information has been compiled by Dipl.-Ing. Konrad Dengler, technical journalist and translator specialized in industrial topics.