ERW tube production: mill revamping strategies for coping with shorter campaigns
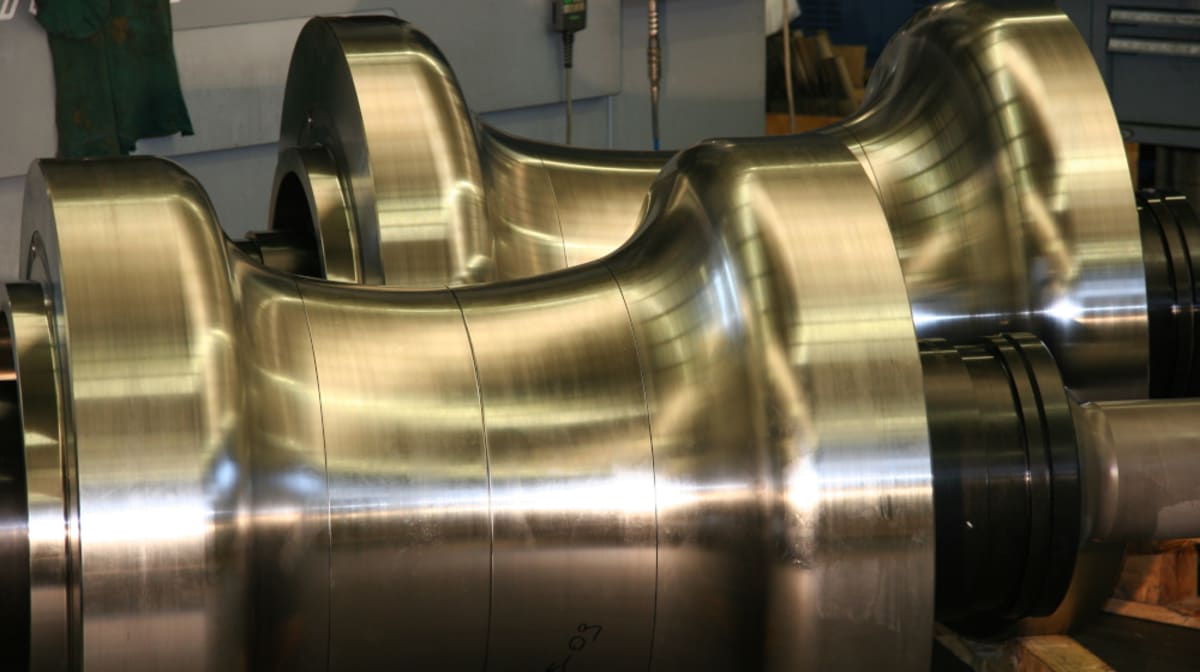
Market evolution has driven manufacturers of electrical resistance welded tubes to reduce the scale of production campaigns. This trend leads to a decline in the operational performance of ERW lines, which are forced to stop more frequently per rolls changeover. To mitigate these negative effects, plant builders have developed more efficient solutions, which must be properly evaluated as they can have significant implications for both plant and operational costs.
Pictured above are rollers for welded tubes up to 28 inches in diameter produced by Eurolls Spa.
Productivity and size of tube production campaigns
The welded pipe market has been evolving for years towards quantitatively smaller production batches. This trend offers several advantages.
Firstly, it allows the warehouse size for finished products to be reduced, resulting in a reduction of the capital employed in the enterprise. The rotation of the warehouse increases, with remarkable financial benefits. In addition, decreased minimum batch sizes favor the shortening of lead times and, ultimately, reduce delivery times for customers.
However, despite these advantages, there are also some disadvantages in terms of production efficiency. The greater rotation of the warehouses requires, in fact, a greater number of diameter changes, with a consequent increase of stops for equipping the welding line. Equipping involves replacing rolls that the line has used to produce tubes of a certain diameter with those suitable for the next diameter in the production program.
The main ERW diameter changeover technologies are described below.
Equipment changeover technologies in ERW tube lines
- For the sake of simplicity, we will summarize the types of roller changeover in groups with similar characteristics.
Roller changeover 'on the line': this is the simplest type for machines of smaller diameters or older machines. The stands and shafts supporting the rollers are single and are not changed except for maintenance. The equipment changeover is carried out by the production operators on the line itself, with changeover times that vary according to the size of the rolls, up to one shift for large-diameter lines. - Rafter change: in this case, the stands supporting the rollers are mounted in groups on plates. For example, the vertical and lateral forming stands constitute a single group; the stands of the finpasses are another group; a third group is the sizing. The welding box is usually changed separately. In this mode, the plates are double, one in line to produce and one on the shop floor. There are, therefore, also double shafts and bearings. The assembly of the actual equipment is carried out offline, in a dedicated area. In this area, specialized and additional personnel must be provided additional to the production staff. With this solution, plant downtime for diameter changeover can be half on medium-diameter lines compared to ‘on the line’ changeover time.
- Cassettes changeover: this is a solution ‘copied’ from rolling mills for flat products. In this case, shafts, bearings, and supports are double. The stands are single; only the stands mounted in line are needed. These are wide enough to pass the entire cassettes through the front window. Also, in this case, specialized personnel are needed to assemble and disassemble the rolls from the cassettes offline. The diameter changeover time is minimized, especially for large-diameter mills. The efficiency is due to the fact that only the groups consisting of roller, shaft, and supports are shifted, that is, smaller weights and encumbrances. However, this solution can be expensive in terms of initial capital investment on medium or small-diameter lines.
Note that the type of changeovers described has little impact on the timing of the insertion of impeders, inner bead removal device, and welding coils. These devices are mounted after the installation of finpass and welding rolls, with installation times that are not negligible at all, particularly for impeders. In the case of changeover with very fast methodologies, the assembly time of the internal bead removal system is one of the most critical.
Pictured above are rolls for welded tube production by FB Rolls.
Rolls changeover and line revamping
Older welding lines feature 'on-machine' rolls changeovers, which are the easiest and most time-consuming mode. To keep up with new trends in production campaigns, it is often decided to revamp the line with superior roll-changing technologies, as the advancement of the technology in the diameter changeover alone does not justify the complete replacement of a line for ERW tubes.
In the case of revamping, the elements to be taken into account shall be at least the following:
- It should not be assumed that the rollers' design, especially the distances between the forming steps or finpass or sizing, is perfectly maintainable. Variations in distances may be necessary, and if this is the case, a technological analysis must be carried out.
- Analysis of available spaces: in general, the 'in-machine' diameter changeover solution is the least critical in terms of space. The other solutions described involve establishing a tooling area where rolls changeovers are performed either on cassettes or on floor plates. The frontal area of the line must accommodate the exchange of old and new rolls.
- The investment required could be substantially affected by ancillary works, civil works as an example. Creating spaces as indicated above may require changes to workspaces.
- A tooling department with specialized personnel is essential, in addition to the line staff.
What tooling solution for your tube welding line?
In conclusion, the choice of the most suitable rolls changeover technology depends on several factors, including the line size, the frequency of diameter changeover, and the available budget. It is important to carefully assess each solution's advantages and disadvantages, taking into account the overall economy of the plant and the cost considerations.
About the author:
With two decades of experience as a plant manager in leading plant and steel companies, Eng. Jacopo Grassino offers high-level consulting on a wide range of industrial aspects. His areas of expertise include cost optimization and maximization of production efficiency, production start-up, definition and implementation of strategic plans for the achievement of business objectives, and team management. If you would like to learn more about his experiences and skills or request personalized advice, please contact him at:
Telephone: +39 3396821463
Email: [email protected]
LinkedIn: https://www.linkedin.com/in/jacopo-grassino/