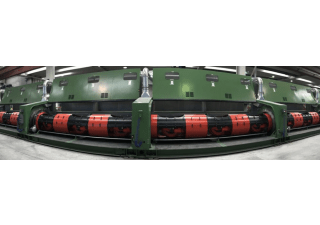
How to make ropes and strands, the basics of rope making
Ropes and wire strands are elements made by twisting together thinner cords or wires. They are mainly used to carry and move loads or to tie things together and find application in several fields including construction, elevators, mining, energy supply, agriculture, logistics.
More about ropes and wire strands. Definition, history and applications >>
Rope making
In the early days, steel wire ropes were made by hand on rope walks where a number of wires were laid out. Workmen equipped with a rotating device walked along the group of wires and twisted them into strands. The process was then repeated with a group of strands, resulting in a rope. This technology had its roots in the manufacture of ropes made of plant materials such as hemp. The strand and rope-making process was gradually mechanized and is nowadays carried out in industrial rope making machines such as tubular stranding machines which consist of pay-off, rotor and bearing assembly, stranding section, haul-off, and take-up. Tubular stranding machines are also more and more used for the closing of ropes because of their greater effectiveness in comparison with cage type stranding machines.
In the first step, cold drawn steel wires are paid off from spools, which are fixed in the tubular part of the machine, and – as the result of the interaction of the longitudinal movement of the wires and the rotational movement of the tubular section – helically wound around a central wire. The result is called “strand”. In the following step called “roping up”, several strands are laid (“stranded”) in a similar way around a central element to become a rope. The central element can be made of steel or other materials such as natural or synthetic fibers and is called "core". It supports the strands and helps to maintain their relative position under loading and bending stresses. During the wire rope manufacturing process, a lubricant is applied and penetrates to the core. The lubrication reduces friction when the individual wires and strands move over each other and protects against corrosion, inside and on the outside surface.
In order to be operational, the ends of a wire rope must be equipped with end connections.
Further design and manufacturing considerations
An important design criterion is the direction of lay, i.e. the direction in which the wires in the strand and the strands are wound around the core. There is a distinction between left hand (“S”) or right hand (“Z”) lay.
In parallel lay strands, the wires of two superimposed layers are parallel, resulting in linear contact. A wire of the outer layer is supported by two wires of the inner layer along the whole length of the strand. There are also cross lay strands where the wires of the different layers cross each other.
Depending on the final use, the properties of strands and ropes can be influenced by stretching and compacting. Based on the design, a wire rope can be made torsion-free. In this case, it is non-rotating under the influence of a free hanging load.
Literature
American Steel and Wire Company: Tiger Brand Wire Rope Engineering Hand Book. New Jersey, 1944.
Greg Davis: Making Rope With A Hand Operated Rope Machine.
http://www.makerope.com/making_rope.php
George Lawrie: The Practical Ropemaker. Belfast, 1948. (Reprint)
http://www.makerope.com/practical_ropemaker.php
A Bibliography of Cordage and Cordage Making
http://www.ropecord.com/new/dl/biblliography.PDF
For helping us compile the information, we thank -Ing. Konrad Dengler, technical journalist and translator specialized in industrial topics.