Machines for electric mobility
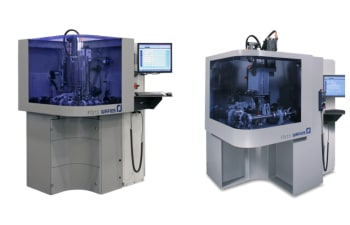
WST Koradi is a renowned Italian spring machine producer and representative of Wafios machine for the e-mobility industry.
Machines for enamelled copper coils - Wafios torsion machines FTU 1.5 and FTU 2.5
FTU Series – Packed with Innovative Technology
The FTU series is particularly suitable for producing simple torsion springs in large quantities due to its favorable unit cost ratio. These springs are used, among other applications, in the automotive and electrical industries, as well as in the home appliance sector.
Flexible application options and shorter setup times
- The new WAFIOS WPS 3.2 EasyCam programming system, convenient and user-friendly, allows for programming sequences with electronic cams. This ensures high usability, short setup times, and flexible application options.
- Significant performance increases guarantee optimized unit costs, especially in large-scale production.
- Maximum quality and repeatability: achieved through an optimized, rigid machine concept.
- High compatibility with existing FTU series toolsets.
- Optional expansion stage: a stripping device can be used to produce copper coils.
Machines for hairpin production (electric motor connections) - Wafios multiformer FMU E
FMU E – revolutionary rotary bending process for hairpin production
The new flexible process allows the production of most hairpin geometries for a stator, including required connection assemblies, in any sequence without tool changes. The patent-pending bending process ensures precise, damage-free bending.
High flexibility with the WPS 3.2 EasyWay programming system
The prerequisite for flexibility is geometric programming of bent parts or hairpins. Geometric programming eliminates the need for operators to individually program CNC axes, thereby accelerating the setup of hairpin geometries. The WAFIOS WPS 3.2 EasyWay control system also supports the automated import of 3D geometries via STEP/IGES files. After importing the coordinates, the required bending program is automatically generated.
Unique machine concept for hairpin production and stator connection assemblies, expanding the FMU series for the electromobility sector
Bending process simulation opens new possibilities, particularly for feasibility assessments or collision checks. The patented hairpin tool system combines active rotary draw bending with the agility of conventional wire bending tools, preventing material slippage toward the tool and enhancing the quality of complex geometries. The newly designed feed unit prevents deformation of the profile material and, in combination with the patented tool system, enables precise positional orientation of the terminal legs. The WPS 3.2 EasyWay programming system stands out for its straightforward geometric programming and clear management of materials and tools used. For a holistic production process, the FMU E series includes modular processes such as stripping, optimized burr-free cutting, and chamfering.
Wafios SpeedFormer transfer line
Wafios SpeedFormer transfer bending system for hairpin large-scale production
The SpeedFormer introduces an entirely new approach to the cost-effective production of hairpins for the latest generation of electric motors. For the first time, the SpeedFormer combines three proven bending processes from the conventional wire and tube bending sectors into a single, comprehensive system. From the wire sector, a bending technology used for decades in WAFIOS coiling, winding, and CNC bending machines has been modified and optimized for hairpin bending. This bending process simplifies the production of hairpins and provides higher production speeds.
Seamless transition from development to large-scale production – identical bending process for prototypes and production systems
Risks in transitioning from prototype production to series production are avoided by fully transferring the production principle of the prototype on the FMU E to large-scale series production. Cycle times on the SpeedFormer for series production are reduced from 6–10 seconds to just 1–1.5 seconds per hairpin. The same production technology is used for both tooling and bending processes.
The advantages of 3D bending without shape-specific tools enable flexible changes between different hairpin geometries without requiring tool changes. This flexibility allows for the production of all hairpin geometries of a stator on a single system, with an economically viable batch size of 1. The full compatibility between systems facilitates rapid project transfers when necessary. The transition from development to series production is seamless, thanks to WAFIOS's consistent production technology for both prototypes and large-scale series. The system delivers high output while maintaining a compact footprint and cost-effective investment. Additionally, quality is assured through integrated testing and control of geometric characteristics, such as leg position or contact surface, utilizing advanced smart camera measurement technology.
Machines for Producing Busbars (Connection Bars)
Wafios BMF Bending Machine - a new way of bending
The BMF series, developed by WAFIOS and controlled by CNC, is a completely new bending machine specifically designed for profiled parts and busbars. It incorporates the latest patent-pending process technologies to create complex parts with the tightest radii and twists. In addition to the traditional straightening, bending, and cutting stages, the system can integrate stripping and twisting processes.
This unique process, tailored for the production of customized busbars in the electromobility sector, highlights a distinctive feature of WAFIOS wire bending machines: the bending process is fundamentally three-dimensional. The wire positioning is achieved by rotating the wire feed, rather than the bending head. The 3D shape (geometry) of the component is produced fully automatically in a single step. Moreover, specific tool solutions have been developed for the use of flat wire, and various machine adaptations have been made to process profiled wire in the areas of feeding, straightening mechanisms, bending spindles, and cutting devices.
The system ensures maximum precision even for the smallest bending radii with minimal bending distances, thanks to a specially designed bending tool (patent pending). The cutting device, designed for flat cables, achieves optimal cutting quality, particularly for busbars (patent pending). The exclusive twisting device enables the production of highly complex bent part geometries and in-process level changes (twisting, patent pending). Productivity is maximized through fully integrated stripping in the production process using a laser device (patent pending). High flexibility during stripping allows for the precise placement of contact points. Additionally, the independent programming station and new flat wire simulation software enable on-site feasibility tests at the customer’s location.
- Macchine varie e accessori •
- Macchine per reti, catene, piegati •
- Macchine per tubi •
- Macchine per lamiera •
- Macchine per molle •
- Avvolgitrici per molle •
- Multiformer per molle •
- Macchine per piegatura e formatura filo •
- Macchine pieganastro •
- Macchine piegatubo •
- Smussatrici per molle •
- Macchine per mollifici