Eco-friendly wire rod preparation lines by Eurodraw: sustainable solutions for the wire industry
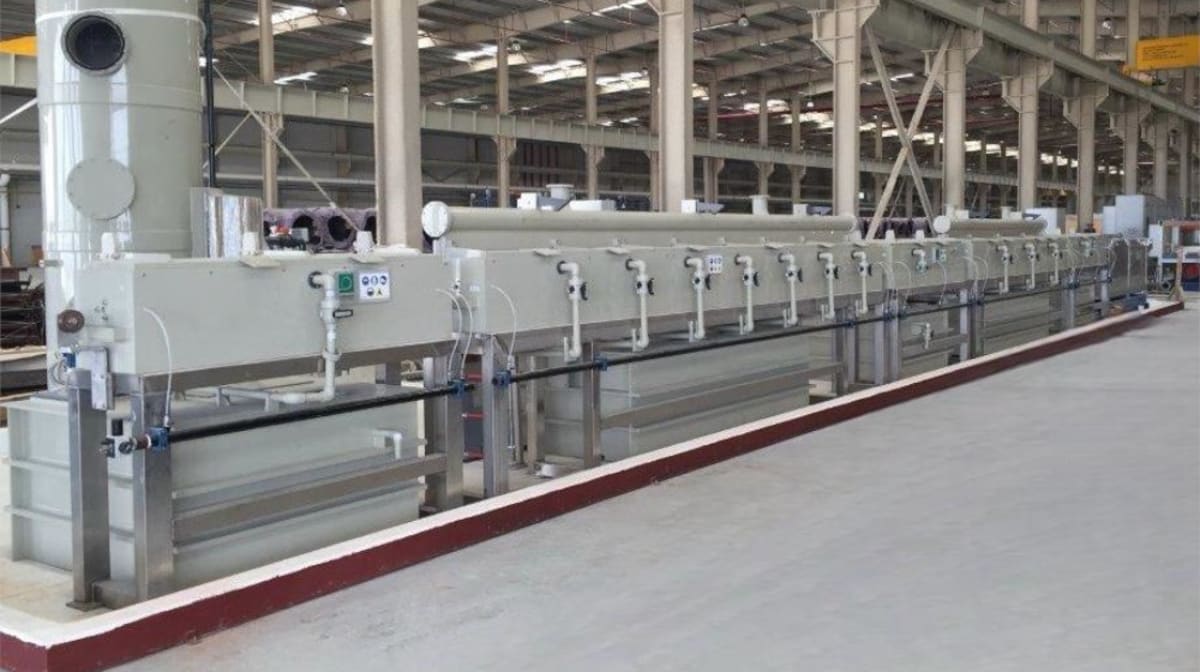
Wire rod preparation for wire drawing has long been a concern due to the effluents generated by the pickling process, which require treatment and disposal. Over the years, there has been a trend towards finding alternative solutions to pickling, particularly for treating high-carbon wire rods.
Eurodraw Wire Equipment, an Italy-based equipment manufacturer for the wire industry, has enhanced multiple solutions to reduce the impact on the environment when processing high-carbon wire rods, without compromising on the wire drawing performances reachable by using eco-sustainable wire rod cleaning and coating systems. The company has developed two different processes:
Acid-free wire rod cleaning system
The first innovation is an acid-free solution designed for wire rods up to 7.00 mm in diameter. It involves a mechanical descaling process using an overheated and pressurized steam cleaner. This process heats the wire rod's surface, allowing the scale layer to expand for easier removal via a reverse bending descaler.
The wire rod then undergoes brushing and rinsing with hot, high-pressure water, pre-heating it to about 80°C before entering the coating tank. Here, an eco-friendly precoating is applied and dried. Coating the hot wire ensures a strong bond, enabling high drawing speeds. This system is environmentally friendly as it doesn't generate effluents; the rinsing water can be filtered and reused after removing iron oxide.
High-carbon steel wire cleaning system
The second system is tailored for larger diameters of high-carbon steel wires, ranging from over 7.00 mm to 16.00 mm. Initial scale removal can be achieved using a shot blaster or a high-speed double belt orbital grinder. This is followed by a high-pressure steam cleaning unit to remove any remaining fine-scale dust on the wire rod surface. High-carbon wire rods typically require phosphate coating or bonderizing.
This line can incorporate the unique E-phosphate coating unit, utilizing a modified zinc/calcium coating applied through a contactless electrolytic process. This process prevents sparks during current transmission, avoiding martensite formation and ensuring product quality. While phosphoric acid is used, it is fully recycled. The rinse waters are reused for various purposes throughout the process, including surface activation and bonderizing solution preparation. The process then proceeds to the coating tank, where an eco-friendly precoating is applied and dried.
Both systems offer wire drawing speeds comparable to traditional batch pickling plants while minimizing environmental impact, reducing energy consumption, and optimizing coating chemical usage for process efficiency.
For more information about Eurodraw Wire Equipment’s technologies, please contact the company through the references on its online stand, or drop by its booth H11/A60 at wire Düsseldorf, from April 15 to 19!
- Rope-making machines •
- Various machines and accessories •
- Wire drawing machines •
- Rope stranding machines •
- Various drawing machines •
- Wet drawing machines •
- Dry drawing machines •
- Pay-off and take-up •
- Cold rolling machines
- Treatment equipment and furnaces •
- Other heat treatment and surface treatment lines •
- Tempering furnaces •
- Pickling lines •
- Galvanizing lines